Moschettoni da arrampicata: quando la meccanica incontra lo sport
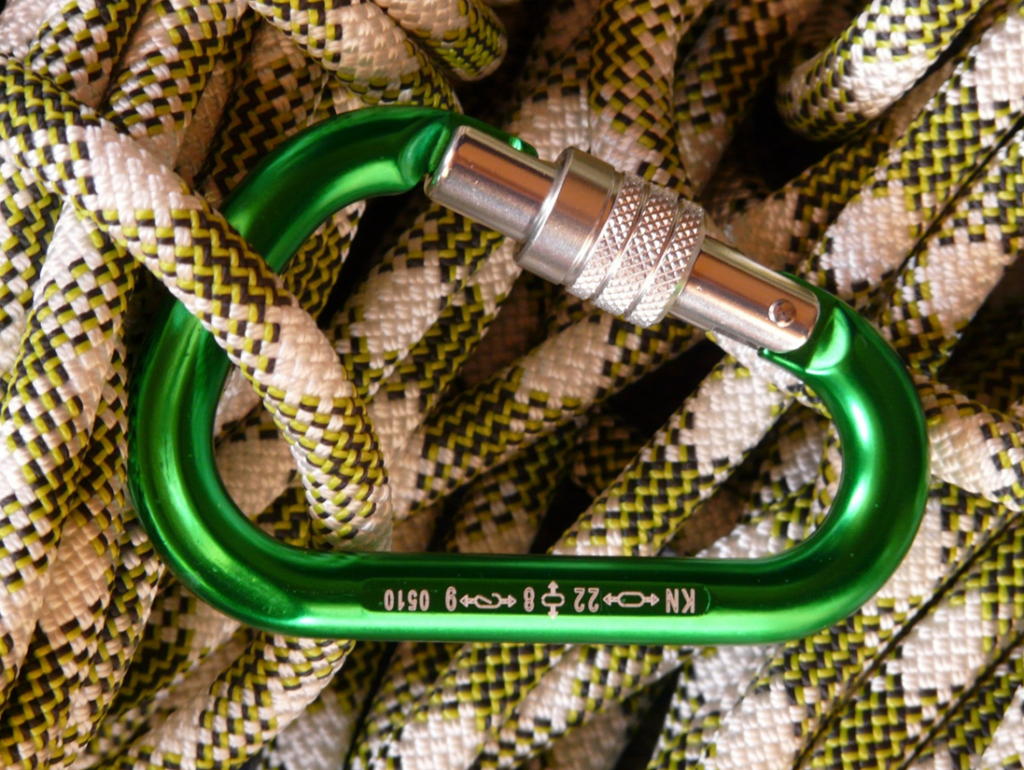
Cosa hanno in comune dei moschettoni da arrampicata e un aereo di linea? Chiaramente una lega di alluminio di grado aeronautico. Perché che stiate volando a 10 000 metri di altitudine o che stiate arrampicando una parete rocciosa, la vostra vita è appesa ad un filo, o meglio, ad una corda.
Moschettoni da arrampicata e standard di sicurezza
Gli alpinisti sanno bene che i moschettoni da arrampicata sono elementi fondamentali della “catena di assicurazione”, tant’è vero che ad ogni loro arrampicata vi affidano le proprie vite. Non a caso questi dispositivi di protezione furono introdotti per la prima volta nel mondo dell’alpinismo da un arrampicatore tedesco, Hans Dülfer, il quale li impiegò nel 1912 per scalare la parete est del Fleischbank nella regione del Tirolo in Austria. In origine i moschettoni consistevano in dei pesanti anelli di acciaio più o meno improvvisati, mentre si dovrà aspettare intorno agli anni ’40 per poter vedere il primo moschettone in lega di alluminio ideato dall’alpinista francese Pierre Allain.
Oggigiorno i moschettoni da arrampicata sono diventati dei complessi prodotti meccanici caratterizzati da elevate prestazioni in termini di sicurezza, soprattutto grazie alle severe norme a cui devono sottostare per poter essere commercializzati. Infatti, ogni moschettone venduto per essere utilizzato in ambito alpinistico deve necessariamente essere conforme alla norma europea EN 12275, la quale prevede una serie di prove meccaniche indispensabili per la garanzia di affidabilità del componente. In particolare, la norma obbliga il produttore a testare la resistenza meccanica a trazione dei moschettoni da arrampicata lungo la direzione longitudinale (asse maggiore), sia in caso di moschettone aperto che chiuso, e trasversale (asse minore). Ogni moschettone a norma deve quindi riportare i tre carichi di rottura ottenuti tramite la prova a trazione nei tre casi sopracitati, fateci caso quando ne acquistate uno.
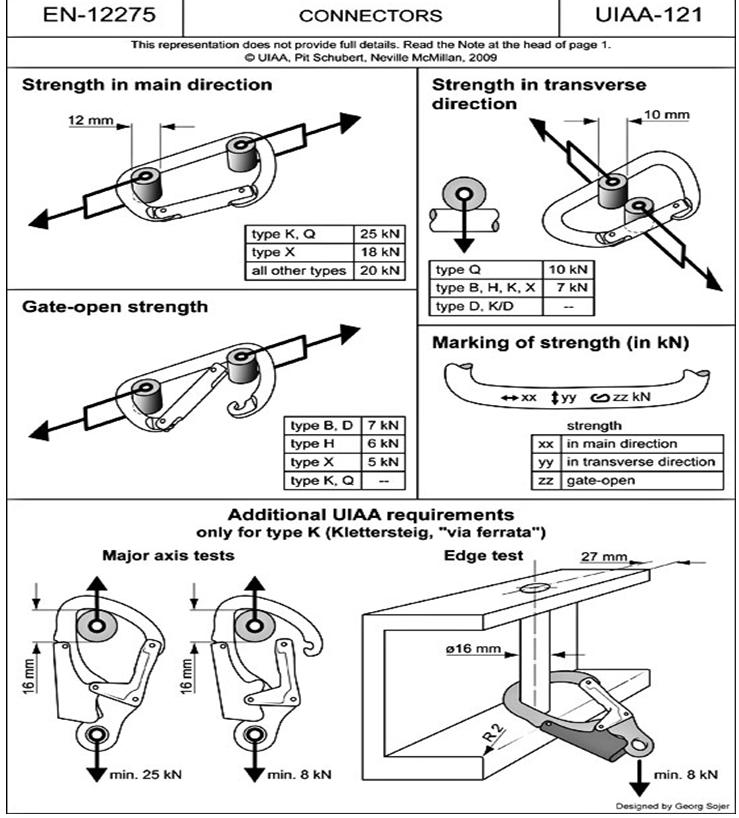
Il caso più critico è chiaramente quando il moschettone è aperto e caricato sull’asse maggiore. Infatti in questo caso la norma prevede una resistenza a trazione minima intorno ai soli 6 kN, anche se quest’ultima può variare leggermente a dipendenza del tipo di moschettone. Come visto nel caso delle cadute in arrampicata, una forza di arresto di queste proporzioni si verifica facilmente in seguito alla caduta di un arrampicatore, perciò è sempre di fondamentale importanza assicurarsi che i moschettoni da arrampicata possano lavorare nelle migliori condizioni possibili, ossia correttamente chiusi. Il caso più favorevole, invece, è quello in cui il moschettone è chiuso e caricato sull’asse maggiore, per cui la norma prevede una resistenza minima intorno ai 20 kN, anche qui il valore può variare in base alla tipologia del moschettone. Forze di arresto di queste proporzioni possono avvenire solo nei casi peggiori, e comunque la rottura del moschettone sarebbe il vostro ultimo problema dato che la forza di arresto massima sopportabile dal corpo umano prima di riportare ferite gravi si aggira intorno ai 12 kN.
La meccanica dei moschettoni da arrampicata
Come detto, i moschettoni sono un complesso prodotto meccanico sia dal punto di vista dei materiali adottati che da quello puramente strutturale. Infatti, partendo dalla semplice sezione circolare del moschettone si è giunti a forme più complesse con una sezione che in alcuni casi è anche variabile lungo tutto il componente. Ma cerchiamo di capire il perché di questa evoluzione di design con un occhio un po’ più attento alla meccanica che si cela dietro a questi dispositivi di protezione.
Se siete degli arrampicatori sapete bene che il peso dell’attrezzatura che ci si porta appresso è un fattore che può diventare determinante durante un’ascesa in parete, o comunque se non lo siete potete ben immaginarlo. Difatti, se vi trovaste a qualche centinaio di metri da terra su una parete verticale, sareste grati per ogni grammo in meno da dover trascinare a forza fin su alla vetta. Per questo motivo i produttori di attrezzatura da alpinismo hanno cominciato a fare un uso più sapiente del materiale a loro disposizione ideando forme sempre più efficienti rispetto alla semplice sezione circolare. Ma come può la sola forma della sezione permettere di alleggerire il materiale senza perdere in resistenza meccanica?
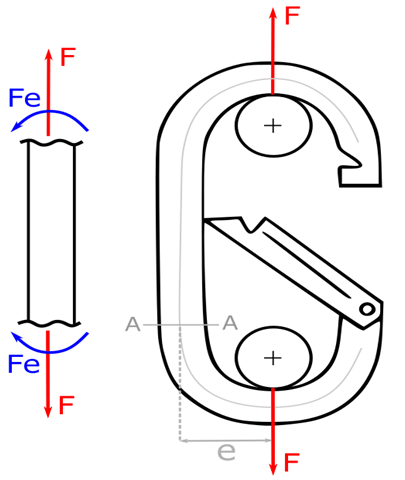
Per rispondere alla domanda dobbiamo ricorrere ad un semplice modello meccanico per approssimare il comportamento a trazione del moschettone. Se consideriamo per semplicità un generico moschettone simmetrico sottoposto ad una forza di trazione lungo l’asse maggiore e aperto, possiamo calcolare l’intensità massima della forza per cui si ha una deformazione permanente. Per fare ciò dobbiamo suppore il moschettone come una trave curva e calcolare lo sforzo dovuto alla forza di trazione F nella sezione più sollecitata (Sezione A-A). Prima di presentare i risultati dell’analisi è bene fare una riflessione sulle sollecitazioni che ci si trova a sostenere. In particolare, la presenza di un’eccentricità del carico rispetto al “corpo” del moschettone provoca un momento flettente che risulta essere il principale responsabile dello sforzo a cui il componente è sottoposto, ma non è l’unico, perché abbiamo chiaramente anche l’effetto della forza di trazione.
Svolgendo i calcoli e confrontando i risultati ottenuti per una sezione circolare ed una sezione ad “H”, possiamo capire perché nei moschettoni più leggeri la forma prediletta è simile a quest’ultima. Nel nostro modello semplificato, a parità di materiale, la sezione ad “H” presenta una resistenza meccanica tre volte superiore rispetto alla sezione circolare, nonostante un’area circa due volte più piccola. Di fatto quello che il modello ci mostra è che utilizzare una sezione più complessa permette di ridurre considerevolmente il peso del moschettone ottenendo allo stesso tempo una resistenza meccanica più elevata. Ciò accade perché lo sforzo prodotto dal momento flettente è massimo nei punti più esterni della sezione e perciò posizionare preferibilmente il materiale all’esterno di quest’ultima (a formare delle flange) permette di sfruttare in modo più efficace il componente.
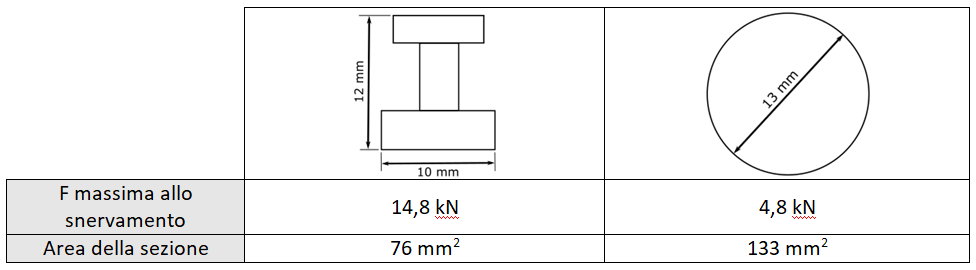
C’è da dire che il modello utilizzato è solamente una prima approssimazione del comportamento reale del componente e deve servire a darci un’idea generale del perché si effettua una scelta piuttosto che un’altra. Difatti, nella progettazione di moschettoni da arrampicata entrano in gioco più fattori che ne possono determinare la geometria, come ad esempio la necessità di predisporre una superficie di contatto sufficientemente curva per la corda oppure la fattibilità del processo di produzione. Senza contare il fatto che i moschettoni moderni presentano forme così complesse che solo una simulazione con un software di calcolo strutturale potrebbe predirne con accuratezza il comportamento a trazione.
Leghe di grado aeronautico per i moschettoni
Fino a questo punto abbiamo considerato solamente l’aspetto puramente strutturale del moschettone, tuttavia a determinarne le prestazioni è prima di tutto il materiale di cui sono fatti. La maggior parte dei moschettoni da arrampicata che si trovano oggi in commercio sono fatti da una lega di alluminio nata per applicazioni strutturali in ambito aeronautico, la 7075 T6. Questa lega, i cui principali elementi alliganti sono lo zinco (Zn), il magnesio (Mg) e il rame (Cu), presenta delle elevate proprietà meccaniche unite ad una bassa densità. L’unione di queste due caratteristiche rendono questa lega particolarmente efficace in quelle applicazioni dove il peso e la resistenza meccanica sono i fattori determinanti, come nel caso del settore aeronautico appunto.
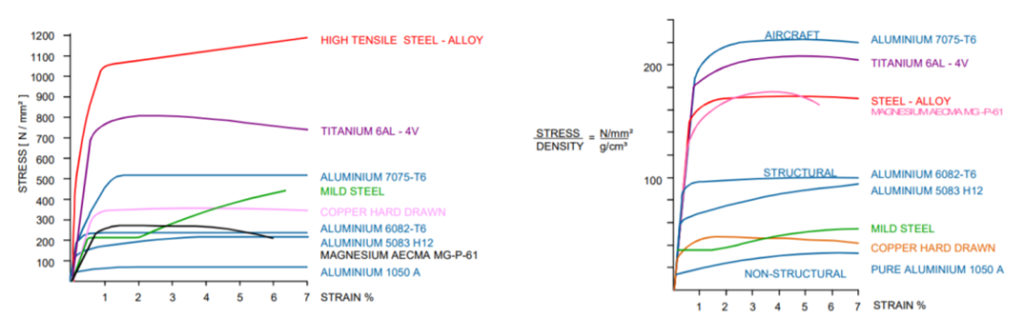
Il vero segreto delle elevate proprietà meccaniche della 7075 T6 risiede però nel trattamento termico a cui viene sottoposta, ovvero la tempra di solubilizzazione con conseguente invecchiamento artificiale. Di per sé la lega non trattata termicamente presenta un carico di snervamento molto basso intorno ai 150 MPa, ma con un adeguato trattamento questo valore può salire anche fino a 500 MPa. L’elevata resistenza meccanica e la bassa densità permettono alla 7075 T6 di competere con le più pesanti leghe di acciaio e le costose leghe in titanio. Perciò che siate su un aereo o che stiate arrampicando, ora sapete a cosa state affidando le vostre vite!
Articolo a cura di Axel Baruscotti