Mercedes AMG One: iniziata la produzione della hypercar, sarà assemblata a mano
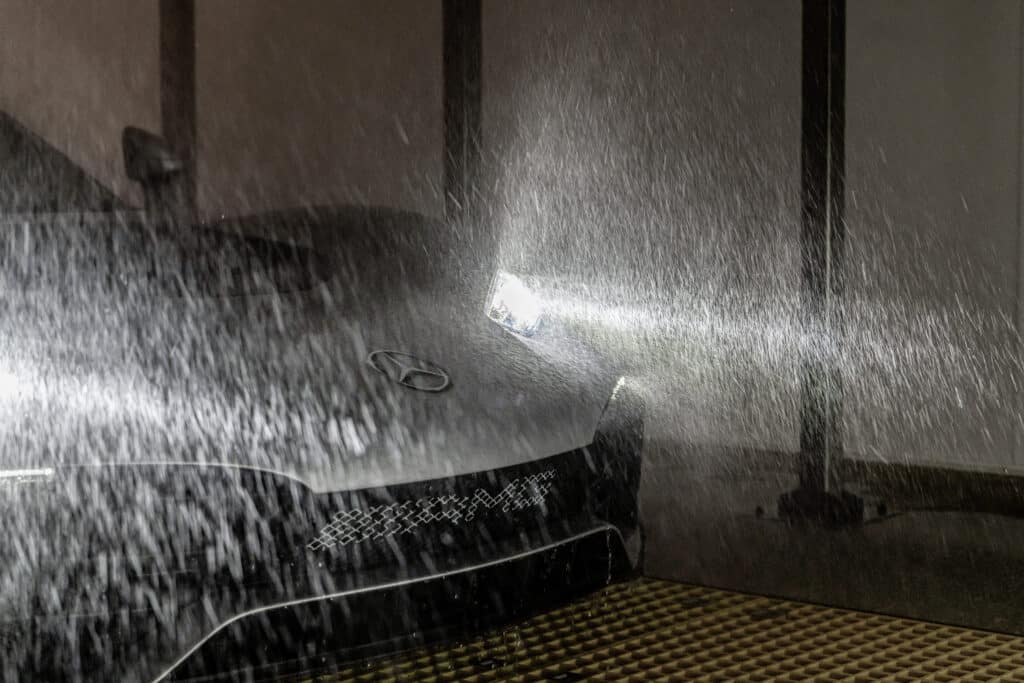
Mercedes AMG One: iniziata la produzione della hypercar, sarà assemblata a mano
Saranno realizzati solo 275 esemplari in totale di Mercedes AMG One. La produzione del primo esemplare è appena iniziata. I primi veicoli per i clienti saranno consegnati nella seconda metà del 2022. Il propulsore ibrido basato sulla Formula 1 con un motore turbo V6 da 1,6 litri e quattro motori elettrici è stato costruito dagli esperti di sport motoristici presso Mercedes-AMG High Performance Powertrains a Brixworth (Inghilterra), che sono anche responsabili dello sviluppo e della produzione delle Power Unit per le monoposto da Formula 1.
“Mercedes-AMG ONE è il progetto più ambizioso che abbiamo mai intrapreso, dallo sviluppo alla produzione. Segna un altro punto culminante nello sviluppo strategico di successo di Mercedes-AMG verso un futuro elettrificato delle prestazioni. La produzione dell’esclusiva serie è un sfida davvero unica. Per la prima volta, l’hypercar porta l’attuale tecnologia ibrida della Formula 1 nella quasi totalità dalla pista alla strada e combina prestazioni travolgenti con un’efficienza senza precedenti. Questo primato mondiale sta diventando realtà grazie alla grande lavoro di squadra tra Mercedes-AMG ad Affalterbach, gli esperti di Formula 1 presso Mercedes-AMG High Performance Powertrains a Brixworth e il nostro partner di produzione Multimatic. Noi come l’intero team siamo molto orgogliosi di aver ora avviato la produzione dei primi veicoli dei clienti”, afferma Philipp Schiemer, Presidente del Consiglio di Amministrazione di Mercedes-AMG GmbH.
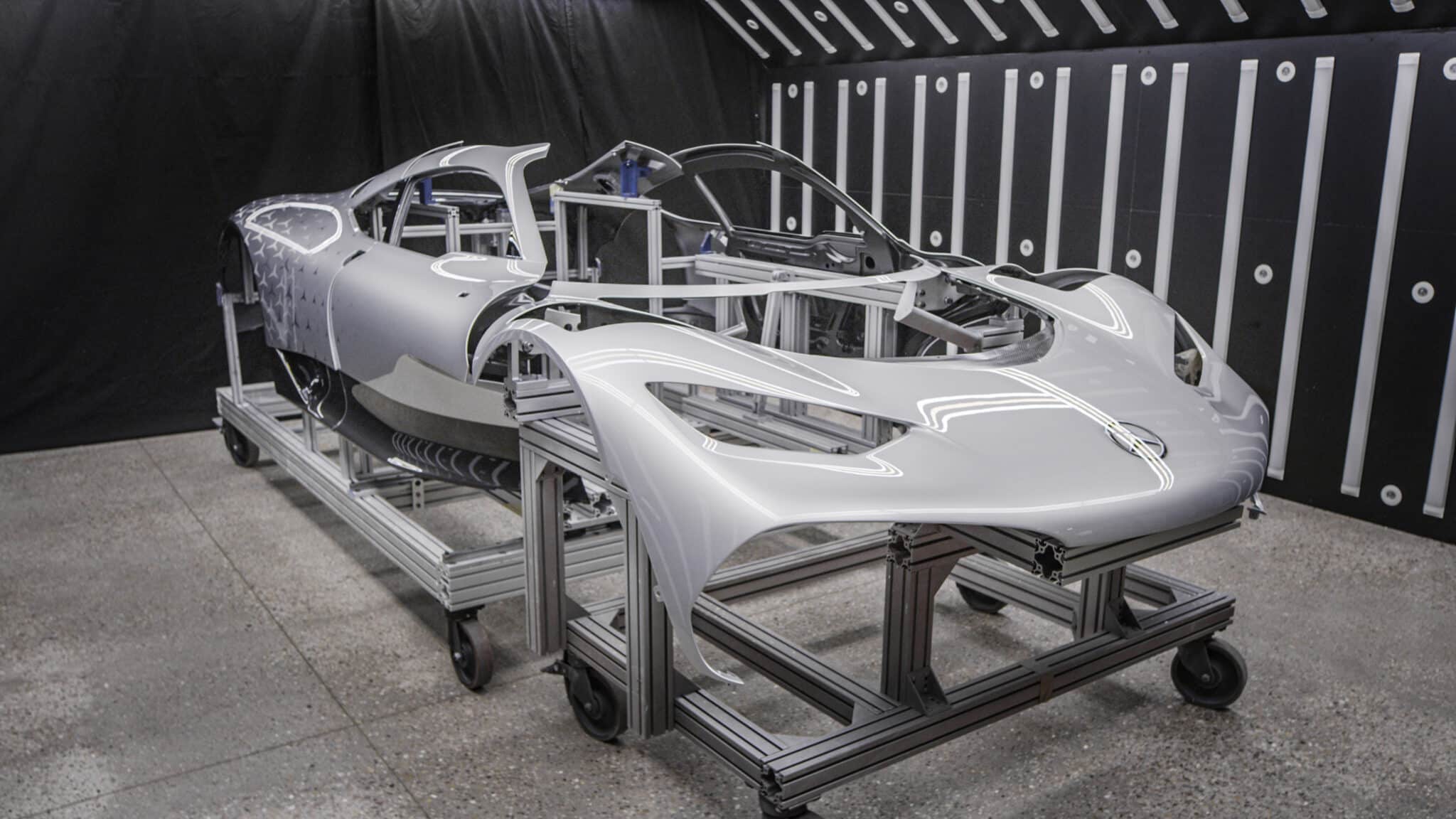
La fase di assemblaggio della Mercedes AMG One
L’esclusiva produzione della AMG One è completata a mano in 16 stazioni di assemblaggio e collaudo. Molte fasi di lavoro ricordano la produzione di orologi di lusso di alta qualità: alcuni sottosistemi vengono prima premontati e testati per il funzionamento, quindi smontati nuovamente e solo successivamente installati nel veicolo. Questo vale, ad esempio, per la monoscocca in fibra di carbonio con tetto incollato e tutte le parti della carrozzeria removibili, anch’esse realizzate con un materiale leggero e stabile, ma anche costoso.
L’intera carrozzeria esterna è la prima ad essere completamente assemblata. Il tutto viene controllato meticolosamente e, se necessario, adeguato di conseguenza. Questo è l’unico modo per creare un modello di giunzione perfettamente uniforme. Nel processo, gli specialisti devono tenere conto della laccatura finale, che aggiunge il proprio spessore al materiale. Dato che lo spessore della parte in carbonio è di soli 1,2 millimetri in determinate posizioni, questo è un compito altamente difficile che richiede degli specialisti. Una volta che tutto combacia perfettamente, le parti, comprese le portiere e i cofani, vengono smontati di nuovo e poi verniciate a mano.
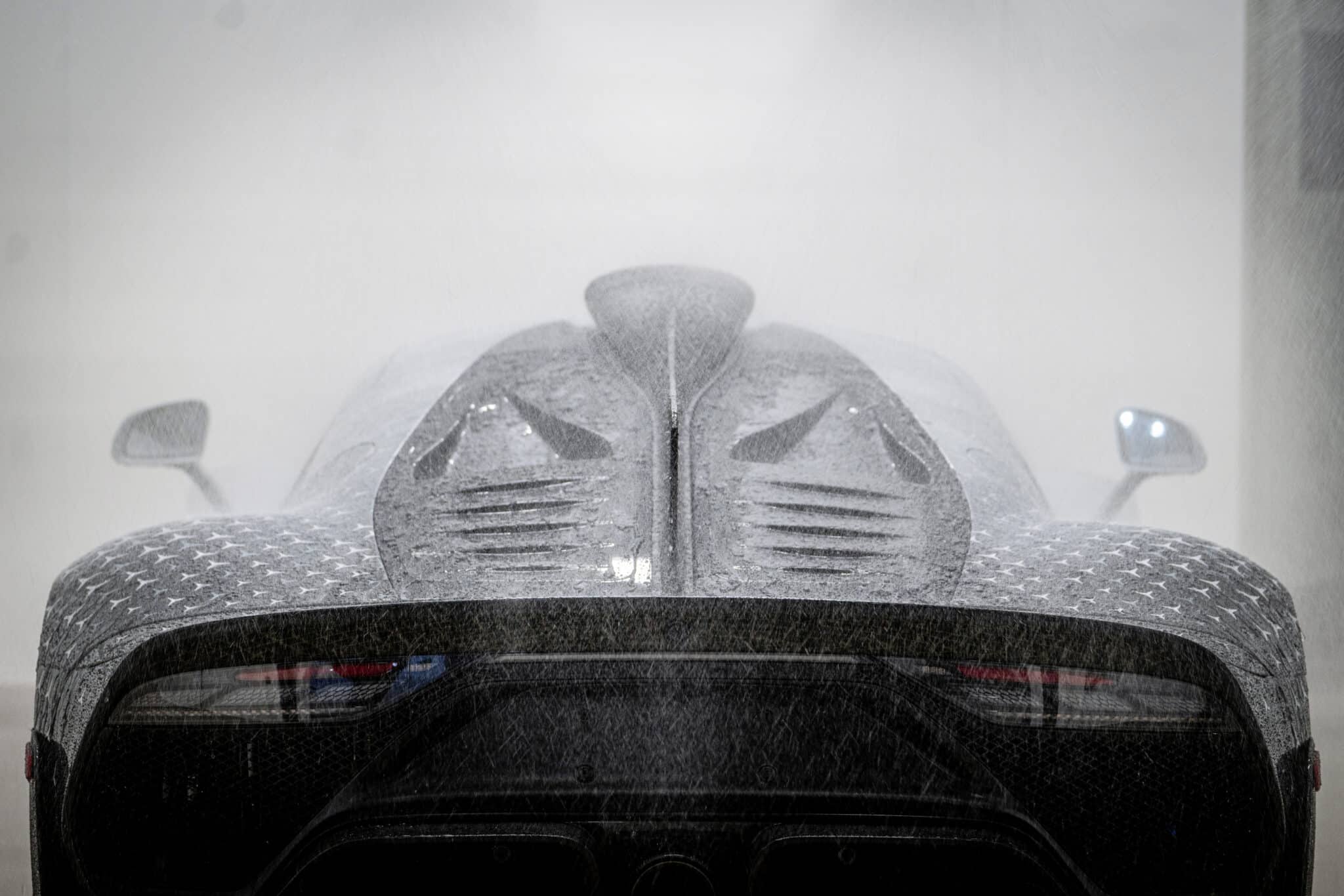
Nella fase di assemblaggio successiva, vengono assemblati il gruppo propulsore e la carrozzeria: il motore turbo V6 da 1,6 litri, la batteria ad alto voltaggio e il totale di quattro motori elettrici sono stati tutti precedentemente testati a caldo sui banchi di prova di Brixworth per garantire che siano sani e performanti, esattamente lo stesso processo che viene seguito con le Power Unit Mercedes di Formula 1. Mercedes-AMG High Performance Powertrains fornisce le unità corrispondenti: il motore a combustione ibrida eTurbo, la batteria ad alto voltaggio dell’ibrido plug-in, l’assale anteriore con due motori elettrici e l’elettronica di potenza compreso l’inverter per ciascuno dei quattro motori. Nel flusso di lavoro, il 75% delle parti è già assemblato prima dell’installazione dei componenti ad alta tensione.
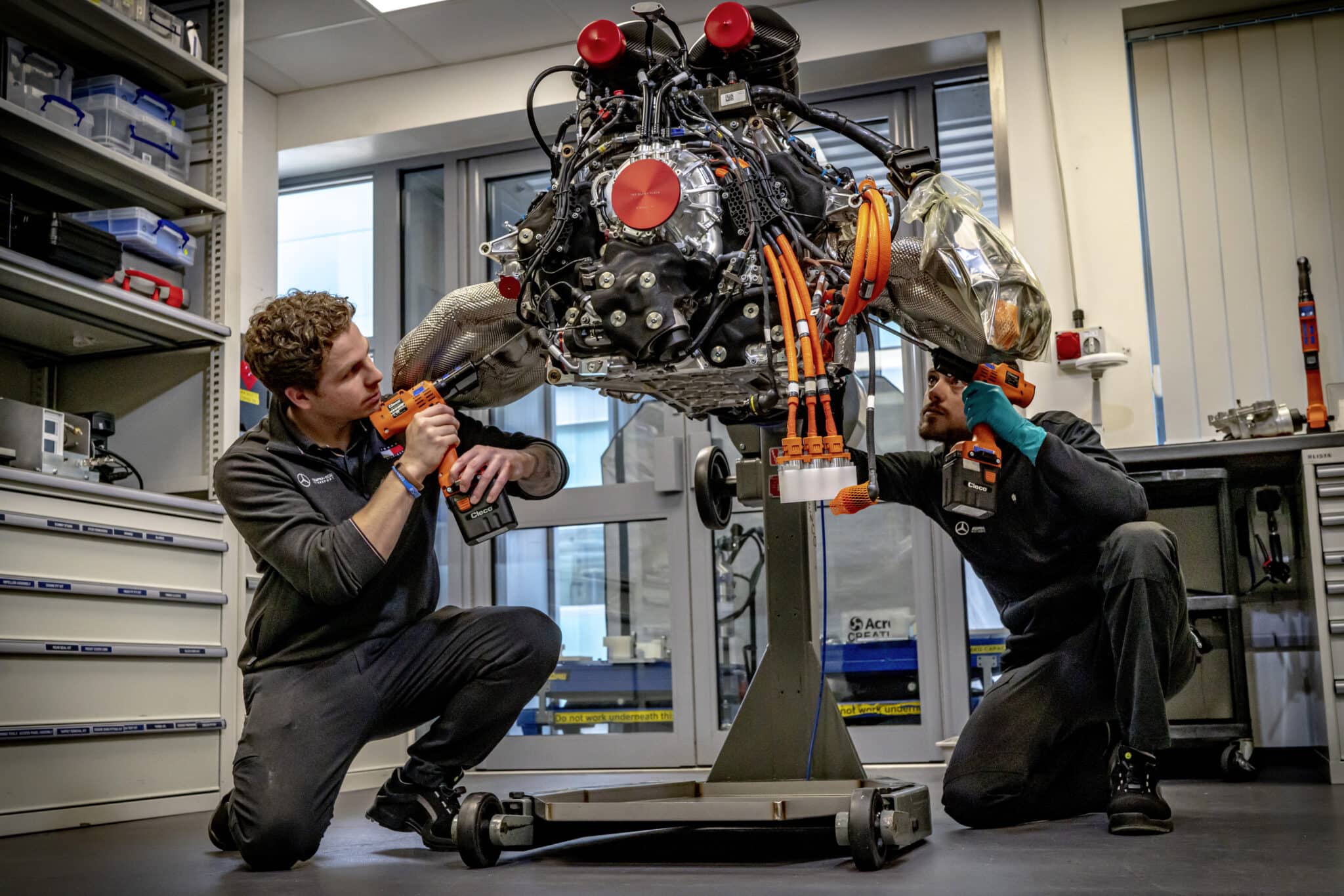
Com’è organizzata la fase produttiva della hypercar
Come già anticipato, la fase produttiva è suddivisa in 16 stazioni. Dalla stazione 1 alla 4, si assemblano le parti meccaniche e tutti i componenti a bassa tensione. Si installano anche i componenti essenziali del gruppo propulsore, compreso l’impianto elettrico del veicolo.
Nelle stazioni 5 e 6 ci si occupa dell’assemblaggio della batteria ad alto voltaggio e dei collegamenti, si effettuano prove di funzionamento del motore a combustione interna e dei motori elettrici. Nella stazione 7 ci si occupa degli interni. Le stazioni 8 e 9 si occupano dell’installazione dei pannelli della carrozzeria: quindi portiere, cofani, paraurti anteriore e posteriore, e simili. Nella stazione 10 viene ultimato in via definitiva l’assemblaggio della carrozzeria. La stazione 11 si occupa del montaggio delle ruote e del pavimento della vettura, mentre la stazione 12 si occupa della regolazione delle ruote e dei fari. Nella stazione 13 troviamo il banco di prova con i rulli per testare il veicolo in varie modalità di funzionamento. La stazione 14 prevede vari test: resistenza, rumore, vibrazioni e, se necessario, qualche modifica a livello di setup. Con la stazione 15 si testa la condizione climatica estrema delle piogge monsoniche, un clima tipicamente tropicale che vede vere e proprie tempeste d’acqua abbattersi sulle città tropicali. Nella 16esima e ultima stazione, i tecnici fanno un’ispezione visiva complessiva dell’auto e di tutte le superfici. Si effettuano anche prove tecniche dei vari componenti.
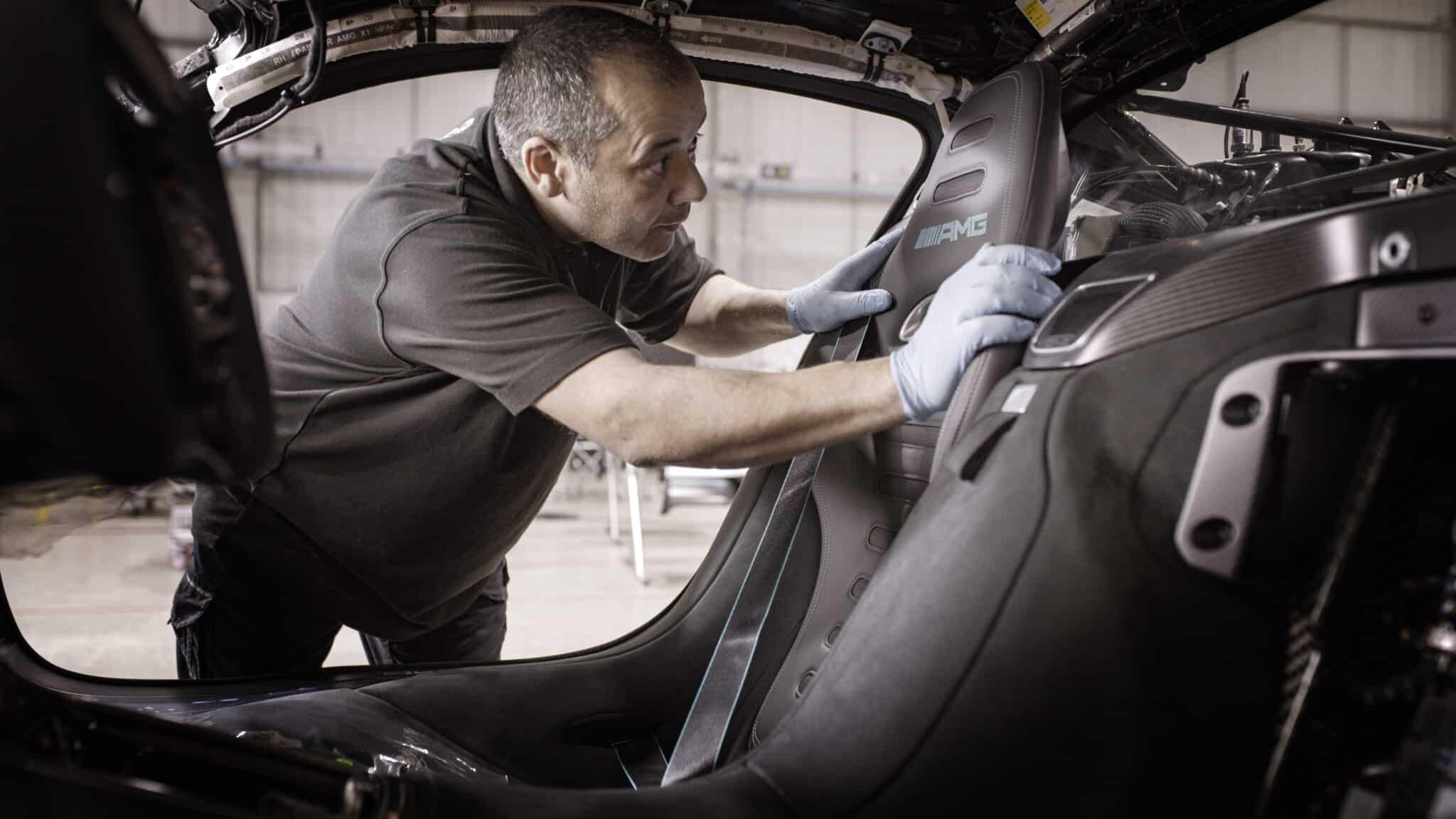
Su ogni singolo esemplare di Mercedes Amg One lavorano circa 50 specialisti. Dopo ogni stazione, ci sono controlli di qualità approfonditi basati su caratteristiche definite, con conseguente ampia documentazione del processo produttivo. Il meticoloso processo di produzione è completato dai più recenti metodi di produzione dell’Industria 4.0, che Mercedes-AMG utilizza anche nello stabilimento di Affalterbach per la produzione di motori AMG. Pertanto, i componenti vengono pre-smistati in set coordinati e sono disponibili esattamente al momento giusto nel posto giusto.
La fase finale della produzione è caratterizzata da un roll-out in un vicino banco di prova, dove ogni Mercedes AMG One viene sottoposta a test di accettazione finale da parte di un collaudatore di fabbrica. Non appena viene data la loro approvazione, il veicolo viene dotato di un’adeguata protezione per il trasporto e trasportato in un autocarro chiuso alla sede Mercedes-AMG di Affalterbach. È qui che si svolgono sia il briefing tecnico del veicolo da parte degli esperti che la consegna del veicolo.
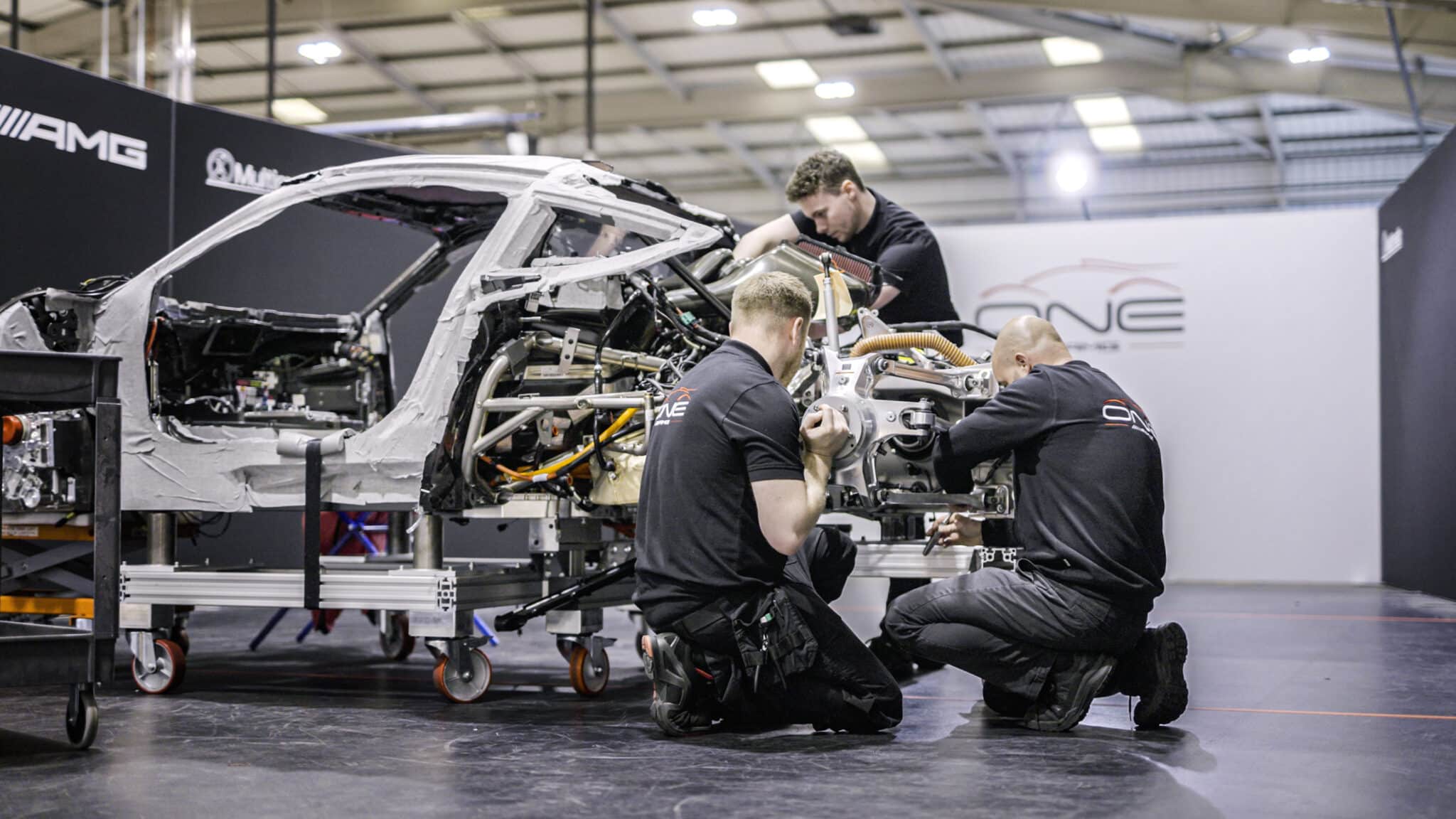