Dischi freno carboceramici: materiali speciali per prestazioni eccezionali
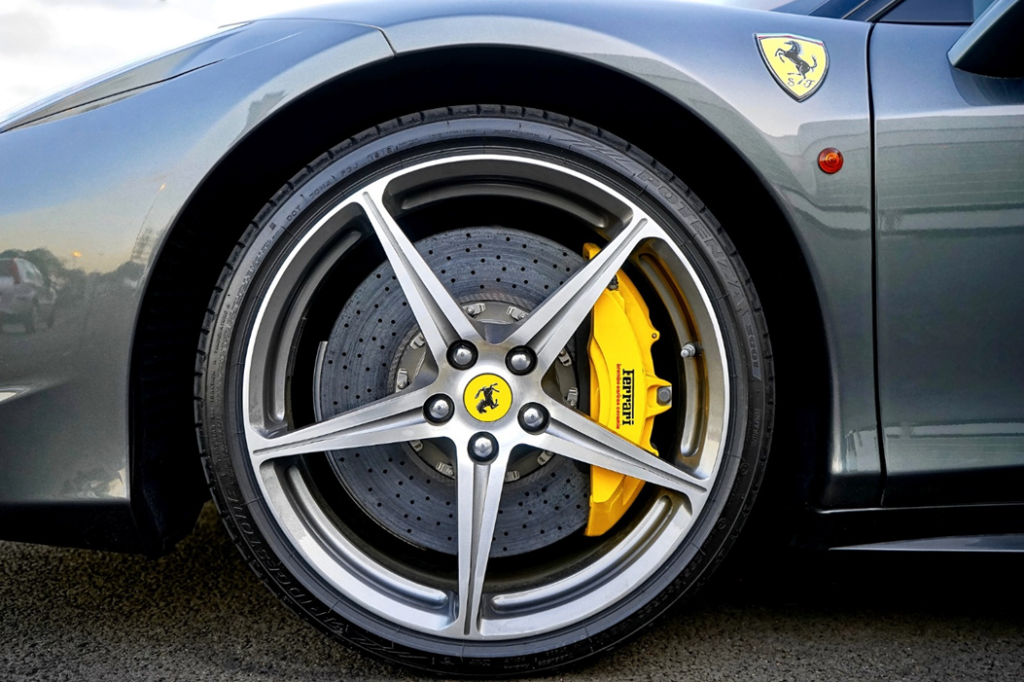
Mikes-Photography
Se siete appassionati di macchine sportive avrete sicuramente sentito parlare dei dischi freno carboceramici, una tecnologia relativamente recente pensata per un parco macchine esclusivo. E’ fondamentale capire come la scienza si celi dietro a questi dischi di ultima generazione.
Dischi freno carboceramici per prestazioni di alto livello
I dischi freno carboceramici fanno parte di una speciale classe di materiali detti compositi a matrice ceramica, spesso abbreviati con l’acronimo CMC. Questi dischi innovativi hanno visto la luce durante gli anni Settanta nel ramo dell’aerospaziale, mentre solo nel decennio seguente sono arrivate le prime applicazioni per il motorsport. Poi, a partire dagli anni Duemila questa tecnologia è sbarcata anche nel settore delle auto sportive riscuotendo un notevole successo, tanto da indurre Brembo, azienda leader negli impianti frenanti, ad aprire una joint venture dedicata allo sviluppo e produzione di dischi freno carboceramici.
Oggigiorno molte autovetture di marchi celebri come Lamborghini, Ferrari, Porsche e Maserati, solo per citarne alcuni, montano questi impianti frenanti di ultima generazione per soddisfare le proprie esigenze di prestazione e design. Non a caso, i dischi carboceramici sono caratterizzati da costi proibitivi che ne giustificano la presenza solamente nel contesto esclusivo delle auto sportive di lusso, ma d’altra parte non poteva essere che così dal momento che la produzione di un disco richiede all’incirca una ventina di giorni a causa del complesso processo produttivo ad alta tecnologia.
Ma vediamo il perché di questa scelta. Rispetto ai tradizionali dischi freno in ghisa, quelli CMC presentano una notevole riduzione di peso che può arrivare anche al 50%. Inoltre, la matrice ceramica possiede proprietà tipiche dei materiali ceramici avanzati, come l’elevata durezza anche alle alte temperature, maggiore resistenza all’usura, basse deformazioni alle alte temperature e ottima resistenza alla corrosione. Tutte queste caratteristiche rendono i dischi freno CMC ideali nel limitare l’effetto del fading, ovvero la perdita di efficacia del sistema frenante in seguito a frenate lunghe o ripetute, e nell’aumentare la vita utile dei dischi. L’ultimo aspetto da considerare, ma non per questo meno importante degli altri, è il fattore estetico che per le auto di lusso rappresenta spesso uno degli elementi trainanti del prodotto. Volete forse dire che il design nero opaco accompagnato dalla texture tipica delle fibre di carbonio di questi dischi non vi cattura?
Vantaggi e svantaggi dei materiali ceramici, il perché dei dischi freno carboceramici
Per capire l’origine dei CMC dobbiamo prima soffermarci a parlare dei loro precursori: i materiali ceramici. I ceramici sono una classe di materiali molto ampia, ma essenzialmente si possono distinguere due famiglie principali in base alle applicazioni: i materiali ceramici tradizionali e quelli avanzati. I ceramici tradizionali vengono usati in applicazioni meno esigenti, come sanitari e stoviglie per intenderci, mentre i ceramici avanzati vengono utilizzati in applicazioni critiche che richiedono prestazioni di alto livello. In generale, i materiali ceramici avanzati possiedono molti vantaggi rispetto alle loro controparti metalliche, fra cui alta durezza e modulo elastico, spesso addirittura superiori a quelli dell’acciaio.
Carburo di silicio (SiC) | Acciaio | |
Durezza Vickers [GPa] | 23 | 1 – 9 |
Modulo elastico [GPa] | 400 | 210 |
Tenacità a frattura [MPa m1/2] | 3 – 6 | 30 – 120 |
Comparazione fra proprietà tipiche di un ceramico avanzato e dell’acciaio. Da notare che le proprietà sono variabili e perciò vanno prese come indicative.
Tuttavia, questi materiali presentano anche un grande difetto: bassissimi valori di tenacità a frattura. La tenacità a frattura è una proprietà fondamentale che può essere interpretata come la sensibilità del materiale alla presenza di difetti (cricche, inclusioni, porosità, eccetera…), ovvero più bassa è la tenacità a frattura e più facile sarà la rottura di un componente in presenza di difetti anche microscopici. I materiali che presentano una bassa tenacità a frattura sono caratterizzati da un modo di frattura fragile, cioè la rottura del componente avviene in modo rapido e senza alcun preavviso. Capite bene anche voi che un’eventualità del genere è assolutamente da evitare in caso di componenti critici come nel caso di dischi freno carboceramici!
I materiali compositi a matrice ceramica
Ora che abbiamo capito quale può essere il limite dei ceramici avanzati per applicazioni strutturali dobbiamo anche parlare della relativa soluzione: i compositi a matrice ceramica. I dischi freno carboceramici sono sostanzialmente composti da una matrice ceramica, solitamente carburo di silicio, e da delle fibre ad alta resistenza in carbonio o sempre in carburo di silicio. Qui è la presenza delle fibre a giocare un ruolo fondamentale nel migliorare la tenacità a frattura del materiale, la quale può arrivare anche a valori maggiori di 30 MPa m1/2 nel caso dei CMC SiC-SiC. Non male se consideriamo che la tenacità del carburo di silicio non rinforzato si aggira intorno ai 3-6 MPa m1/2, un miglioramento di circa sei volte!

La forza di questi materiali compositi, rispetto alla controparte ceramica non rinforzata, sta proprio nel possedere un comportamento pseudo-plastico simile ai materiali metallici, anche se comunque sempre molto inferiore, ma sufficiente per evitare una frattura fragile incontrollata. Ciò è visibile nella curva sforzo-deformazione del CMC in cui l’area del sotto-grafico, rappresentante la tenacità del materiale, è molto più ampia rispetto al ceramico non rinforzato.
I meccanismi di rinforzo nei CMC
Ciò che rende possibile il rinforzo dei CMC è l’interazione fra le fibre e la matrice ceramica, in quello che in gergo tecnico viene chiamato bridging mechanism. Sostanzialmente nell’istante in cui la matrice cede sotto il carico esterno si ha la formazione di alcune fratture microscopiche, dette cricche. Normalmente, sotto l’azione di un carico critico, queste cricche crescerebbero rapidamente e in modo incontrollato portando ad una frattura fragile del componente meccanico, tuttavia, in presenza delle fibre la propagazione della cricca è rallentata da una serie di meccanismi di dissipazione energetica. Il primo di questi consiste nel forzare la ramificazione della cricca lungo le fibre indebolendo preventivamente l’interfaccia fibra-matrice con un apposito rivestimento, tale meccanismo è detto debonding.
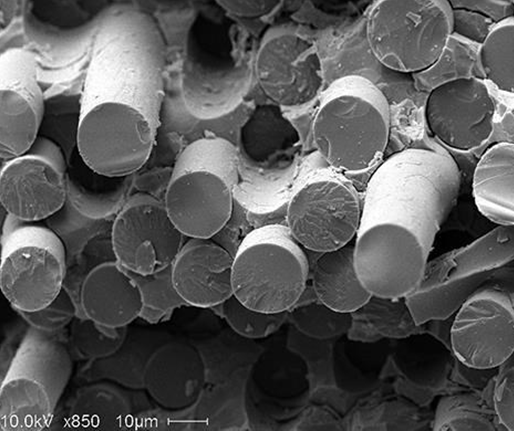
Il secondo meccanismo è la rottura della fibra, il quale richiede una notevole quantità di energia dal momento che le fibre possiedono un’elevatissima resistenza meccanica anche intorno ai 3-4 GPa se si parla di fibre di carbonio o SiC. Per darvi un’idea un acciaio ad alta resistenza arriva intorno a poco più di 1 GPa. Il terzo ed ultimo meccanismo è il cosiddetto fiber pullout, ovvero la separazione completa di fibra e matrice contro l’azione dell’attrito.Il risultato finale è quindi un materiale che unisce le elevate proprietà meccaniche della matrice ceramica con un comportamento pseudo-duttile simile ai materiali metallici.
Articolo a cura di Axel Baruscotti