Dischi freno: dalla ghisa ai compositi
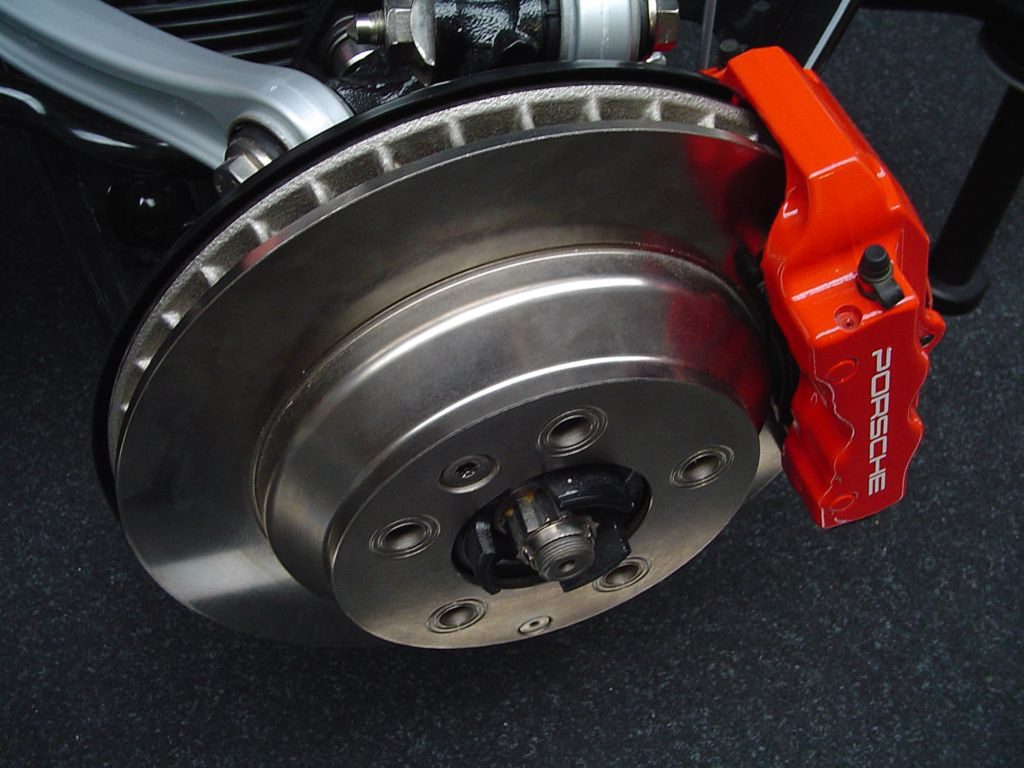
red-live.it
I dischi sono un componente fondamentale per gli omonimi impianti frenanti, detti appunto freni a disco. Questi sono composti da un disco che ruota solidale alle ruote. Al momento della frenata una pinza si stringe sui lati del disco che viene bloccato. I dischi, escludendo quelli in acciaio di applicazione motociclistica, possono essere realizzati utilizzando tre diversi materiali: la ghisa, il carbon–carbon o il carbon–ceramico. Ogni materiale naturalmente ha caratteristiche diverse e viene scelto in base all’uso che si desidera fare dei dischi.
Dischi in ghisa: modesti ma economici
La ghisa è il materiale più utilizzato per la produzione dei dischi freno ed è stato anche il primo ad essere introdotto. Questi prodotti sono montati sulla totalità dei veicoli commerciali e su gran parte delle auto stradali. Sostanzialmente un disco viene prodotto per fusione, successiva solidificazione e verniciatura finale. L’intero processo non richiede più di un paio d’ore, elemento fondamentale per la grande produzione. I materiali prescelti sono ghise grigie lamellari che possono essere ad alto o basso tenore di carbonio.
I principali vantaggi dei dischi realizzati in ghisa sono senz’altro l’economicità e la rapidità di produzione. Inoltre il processo industriale di produzione non è particolarmente complesso. Se consideriamo un mercato legato alle normali auto stradali le prestazioni di questi componenti sono pienamente sufficienti, anche se non elevate. Particolare non trascurabile è la possibilità di utilizzare l’impianto frenante anche a freddo, senza doverlo prima portare in temperatura. Naturalmente non sono esenti da svantaggi in quanto le caratteristiche chimico-fisiche non sono delle migliori. Il disco ha tendenza a deformarsi e bassa resistenza alla corrosione. Di contro, la conducibilità termica è buona.
Composito carbon-carbon
Si tratta della prima alternativa ai dischi realizzati in ghisa ed è stato introdotto alla fine degli anni ’70. La prima applicazione è stata di tipo militare: serviva infatti per i freni dei carrelli dei jet in atterraggio. In seguito l’idea è stata estesa agli aeri di linea e solo dopo anni è approdata in ambito automobilistico con la Formula 1. Ad oggi si tratta ancora di un prodotto di nicchia utilizzato nel mondo delle corse (Formula 1, Moto GP e pochi altri).
Si tratta di un materiale composito formato da una matrice in carbonio rinforzata in fibra di carbonio. Si parte tessendo la fibra di carbonio formando un feltro a bassa densità. Per aumentare questo parametro viene immersa in una sospensione liquida di carbonio (pece). In seguito la cosiddetta “preforma” viene investita da un flusso di Metano a temperatura e pressione ben definite. Sulla superficie rimane così del carbonio amorfo che costituisce la matrice. Infine sono previsti trattamenti termici e antiossidanti.
Vantaggi e svantaggi
Il problema è che questo procedimento è molto lungo e produrre un disco di questo tipo richiede dieci mesi. Questo perché è importante evitare che il carbonio della matrice si depositi solo in superficie e non avvolga tutte le fibre. I vantaggi di questi dischi sono la sue estrema leggerezza e la bassa espansione termica. Le proprietà di questo materiale sono direzionali e il carbon-carbon può essere progettato in base alle necessità per quanto riguarda la conducibilità termica. La procedura di diverso orientamento delle fibre avviene già nel feltro tramite degli aghi e viene detta “needling“. Il coefficiente di attrito di questi dischi è molto alto, così come la resistenza alla corrosione. Tutto ciò garantisce costanza nei rendimenti ad alte prestazioni.
Purtroppo il processo di produzione è molto lungo ed elaborato e i dischi presentano notevoli problemi di usura. Il carbon-carbon infatti non è un materiale duro e va spesso sostituito. Presenta inoltre difficoltà nelle prestazioni a freddo e sul bagnato. Infatti il coefficiente di attrito scaldando i freni aumenta di cinque volte e di dieci se consideriamo la temperatura limite di frenata. Per tutti questi motivi sulle automobili stradali non è possibile adottare questa soluzione.
Composito carbon-ceramico
Viene introdotto alla fine degli anni 90 ed è un materiale composito con una matrice ceramica in carburo di silicio e un rinforzo in fibra di carbonio. Le sue applicazioni principali sono le auto stradali di lusso e/o sportive. Non viene utilizzato in ambito racing, ad esclusione di alcuni campionati monomarca. I suoi principali vantaggi sono la bassa densità e la bassa espansione termica. Il coefficiente di attrito è invece molto alto, così come la resistenza alla corrosione. Le sue prestazioni sono ottime anche a freddo, è stabile fino a 1300°C e resiste allo shock termico fino a 1700°C. Purtroppo anche in questo caso il costo è decisamente elevato e la conducibilità termica non è ottimale, seppur sufficiente.
Il processo produttivo
Mentre la matrice ceramica rappresenta la parte dura del materiale, la fibra di carbonio rende il disco molto elastico ed è distribuita in modo casuale. Essa consente alla struttura di non cedere per schianto poiché assorbe il più possibile l’energia liberata da eventuali cricche nella matrice ceramica. Il processo produttivo si compone di sette step. Viene per prima cosa realizzato un mix delle materie prime a freddo: fibra di carbonio e resina fenolica in polvere. Il tutto viene posto in uno stampo in Alluminio e pressato a caldo (150°C): intorno ai 110-120°C il materiale polimerizza. A questo punto si realizza la pirolisi: in presenza di azoto o argon viene riscaldato il disco che perde il 50% in resina come gas e il 20% in peso. Resta così il carbonio amorfo che poi formerà il carburo di silicio.
Nelle porosità appena formate infatti viene fatto penetrare del silicio fuso a 1420°C che reagisce con carbonio amorfo e si forma il carburo di silicio. La fibra di carbonio a 450°C diffonderebbe come gas: per questo è necessario applicare un trattamento antiossidante tramite un sale. Infine vengono effettuate lavorazioni meccaniche per eliminare le asperità, viene montata la campana per il montaggio e vengono effettuati i controlli.