La fonderia: dagli scarti all’innovazione. Parte 2
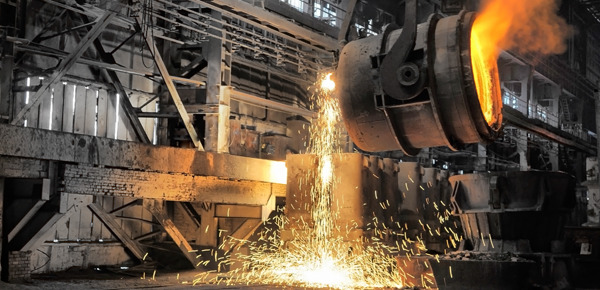
Ph.: innovationclub.it
Riprendiamo quanto detto nella parte 1 sui sistemi di colata:
Le sezioni dei canali prevedono sistemi pressurizzati per tenere in costante alimentazione il flusso di metallo da colare, a questo punto il fattore determinante è il tempo; si dimensiona il sistema di colata dando dei nomi referenziali alle sezioni e alle azioni:
SC: sezione del canale di colata;
SD: Sezione canale distributore;
SA: Sezione degli attacchi di colata;
SA-SD-SC sono sistemi pressurizzati.
Il tempo:
TR: Tempo di riempimento < min(TC, TS);
TC: Tempo critico all’esposizione della forma all’irraggiamento;
TS: Intervallo temporale compreso tra l’inizio della colata e l’inizio dello stadio di solidificazione.
La velocità di riempimento oltre alla forma da definire è influenzata da forze fisiche, risulta facile capire che le forze saranno di tipo conservative e nel particolare in particolare l’energia potenziale gravitazione e l’energia cinetica; trascurando gli attriti e applicando la Legge di conservazione dell’energia meccanica abbiamo: V= √𝟐𝐠𝐡
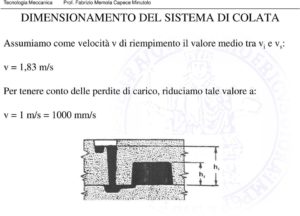
Ph.: docplayer.it/
Piano divisorio
Serve per estrarre il modello solidificato dalla forma senza arrecare danni, se la forma possiede pezzi fragili o geometricamente sottili, è possibile che il metallo si danneggi.
Se non fosse possibile individuare un piano divisorio, si ricorre ad altri metodi per risolvere il problema:
- MODELLO SCOMPONIBILE: Il modello viene ottenuto parte per parte e poi assemblato;
- INSERIMENTO DI TASSELLI;
- MODIFICA DEL PROGETTO: Utilizzato quando il pezzo preso in esame non ha il piano divisorio coincidente con l’asse centrale del progetto.
Ritiro volumetrico
Genericamente le proprietà dei metalli legano l’aumento della temperatura alla modifica della loro forma, infatti vengono fusi si espandono: in primis le molecole hanno un moto rotazionale e vibrazionale e con l’aumento della temperatura e l’avanzare del tempo i metalli subiscono un passaggio di stato e di forma.
A solidificazione avvenuta si verifica il fenomeno di ritiro volumetrico che è dovuta sia alla differenza di temperatura tra la temperatura di colata e quella ambiente, sia come una decrescita dell’energia cinetica delle molecole che passano dallo stadio di dinamicità allo stadio di staticità, come conseguenza il getto tenderà a rimpicciolirsi e quindi sarà più piccolo della forma.
Perciò le dimensioni della forma devono essere maggiorate rispetto a quelle del greggio. Per tenere conto di quanto il getto si contrae, vengono utilizzate delle tabelle che stilano una classifica di ritiri in funzione del materiale e della dimensione del getto.
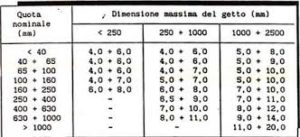
Ph.: www00.unibg.it
La materozza
E’ un “serbatoio” di metallo liquido la cui funzione è quella di alimentare il modello fino alla solidificazione prevenendo e/o addirittura evitando il fenomeno di ritiro volumetrico.
Tipi di materozza:
- APERTE: Strutturalmente è situata sopra al modello ed è in costante e diretto contatto con la pressione atmosferica;
- CIECHE: Sono contenute all’interno della forma e il contatto con la pressione atmosferica è eseguita da un pezzo di materiale poroso situato ad incastro sopra la materozza.
La solidificazione avviene dall’elemento avente modulo minore. A solidificazione avvenuta, il modello viene sgretolato e la materozza eliminata tramite lavorazione meccanica.
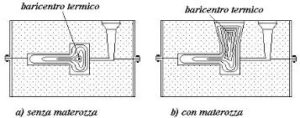
Ph.: acotekno.altervista.org
Portate d’anima
Nel processo di formatura vengono previste le portate d’anima nella geometria del modello. La loro funzione è quella di creare punti d’appoggio per anime e tasselli. L’anima rappresenta il modello delle superfici interne ed è inserita nella cavità dello stampo prima dell’operazione di colatura.
Genericamente è un’operazione che si ricava nella forma da riprodurre effettuata nelle terre e sabbie da fonderia che vengono modellate nelle casse d’anima.
L’esatta misura consiste in un semplice calcolo geometrico:
Lportataanima= 0.3(valore costante) *Lpezzo
Lanima = Lpezzo +2(Lportataanima).
Angoli di sformo
Per agevolare l’operazione di sformo, quindi l’estrazione del costrutto dalla forma, i modelli sono costruiti in modo da evitare o ridurre al minimo le superfici perpendicolari al piano divisorio, per effettuare questo si creano gli angoli di sformo, si tratta di angoli inclinati di α rispetto la perpendicolare.
Durante la creazione del modello si devono evitare gli spigoli vivi perché essendo accumulatori di tensioni meccaniche negative è possibile che il pezzo si danneggi, allora si opta per produrre raggi di raccordo che in seguito, durante i lavori di perfezionamento verranno dimensionati.
Solidificazione
Durante la fase di raffreddamento il metallo tende a contrarsi e per questo la dimensione della forma viene aumentata.
Questa contrazione è nota come “CAVITA’ DI RITIRO” e deve essere evitata perché causa difetti geometrici e funzionali sul prodotto finito.
Il modulo di raffreddamento, trattasi del rapporto tra volume del getto e superficie di scambio termico, influisce proprio sul tempo di solidificazione del getto incandescente.
Due getti con lo steso modulo di raffreddamento hanno lo stesso tempo di solidificazione.
Lo strato solidificato segue una legge che lo relaziona ad una costante ed ovviamente al tempo:
X=K√T
Dove:
k= Variabile dal materiale che costituisce la forma;
X= Spessore del solidificato;
T= Tempo di raffreddamento.
Sovrametalli
Il metallo dopo essere stato fuso, colato, passato nuovamente allo stato solido e raffreddato, viene finalmente estratto dalla forma.
Il risultato finale non è però perfetto, infatti il pezzo possiede oltre ad una rugosità superficiale non indifferente, canali usati nella colata e sbavature varie note come “SOVRAMETALLO”
Lo stadio finale del processo di fonderia prevede la pulizia dei pezzi ottenuti tramite macchine utensili come ad esempio il tornio, il trapano per la foratura e fanno entrambi parte del metodo per asporto di truciolo, in estremis per i canali si opta per troncatrici o, seghe a nastro si usano le fresatrici qualora il pezzo abbia delle scanalature.
Queste operazioni oltre a rendere migliore l’estetica, hanno il principale ruolo di definire la geometria del costrutto per renderlo idoneo alla funzione per cui è stato pensato e costruito, e servono a ridurre i costi, gli sprechi di materiale, (Solitamente gli scarti vengono messi da parte e rifusi) e caratteristiche tecnologiche tali da garantire una certa sicurezza nei confronti degli errori di formatura.