La fatica nei materiali: cause e conseguenze
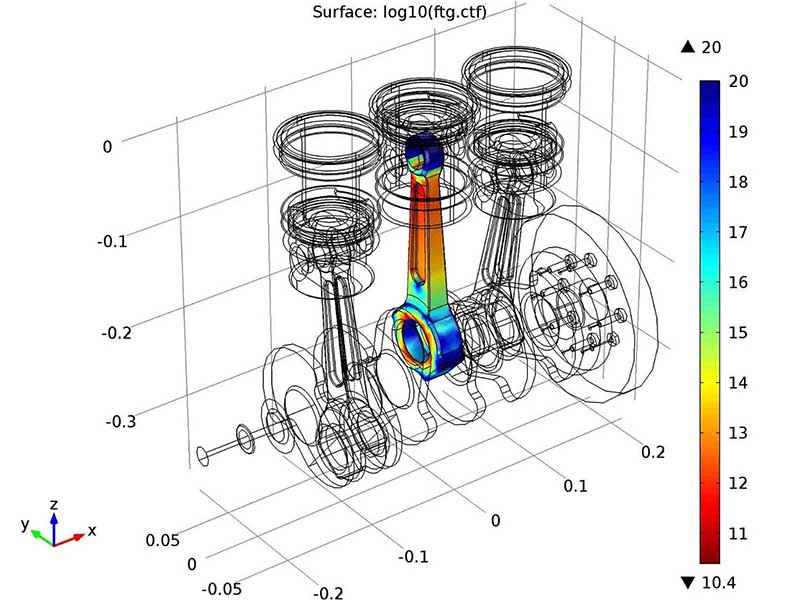
comsol.it
Articolo a cura di Alessandro Vulpio
I materiali, nel corso della loro vita, subiscono uno stress che con il passare del tempo, può danneggiarli irrimediabilmente. Il fenomeno della fatica nei materiali è dovuto all’applicazione di sollecitazioni variabili nel tempo. La sua pericolosità è dovuta al fatto che queste sollecitazioni sono al di sotto della resistenza del materiale. Infatti, se applicata singolarmente, una di queste sollecitazioni non produrrebbe alcun danno. Le rotture dovute alla fatica costituiscono il 90% dei casi di rotture in esercizio. Spesso tali rotture, a causa della loro natura improvvisa, hanno provocato disastri, spesso con perdita di molte vite umane.
Studio del fenomeno
Sin dai primi dell’800 ci si era accorti di questo comportamento, se vogliamo, inusuale ed imprevedibile dei materiali; l’avvento della rivoluzione industriale ha spinto i materiali da costruzione a superare i limiti conosciuti fino a quel tempo. È stato August Wohler, ingegnere tedesco, a studiare i fenomeni di fatica che si verificavano su materiali metallici; realizzò la prova a flessione rotante i cui risultati sono riportati in grafici (curve di Wohler); essi correlano l’entità della sollecitazione applicata al numero di cicli che portano a rottura il componente.
Descrizione fenomeno
I materiali metallici da costruzione sono in genere costituiti da cristalli coesi gli uni agli altri. I cristalli sono a loro volta composti da piani atomici impilati. Il fenomeno della fatica nasce, a livello microscopico, proprio dallo scorrimento irreversibile di questi piani. Sulla superficie di un componente sollecitato nascono quindi dei micro intagli, in corrispondenza dei quali il valore della sollecitazione aumenta a tal punto da provocare l’innesco di una frattura.

L’entità di questa frattura, più comunemente detta cricca, aumenta col passare del tempo facendosi strada all’interno del componente. Questa fase non è accompagnata in genere da nessuna anomalia o deformazione a livello macroscopico, e pertanto è difficilmente apprezzabile dall’occhio umano a meno di controlli specifici. La superficie di frattura si estende, la sezione del componente in grado di resistere alla sollecitazione si riduce; se non riesce più a sopportare il carico applicato, o per un sovraccarico, la rottura avviene di schianto.
La superficie di frattura di un componente rotto a fatica si presenta così:

Nel disegno schematico si nota una zona in cui la cricca è avanzata, che è caratterizzata da una serie di linee (dette linee di spiaggia) concentriche al punto di innesco, e una zona in corrispondenza della quale il materiale si è rotto di schianto.
Discontinuità, intagli o elevata rugosità superficiale, offrono facili punti di innesco di cricche che possono portare alla rottura per fatica. Per questo motivo i progettisti sono in genere molto attenti a questo tipo di comportamento dei materiali. Questo perché, come si suol dire, lo stupido impara dai propri errori mentre il furbo da quelli degli altri. Abbiamo infatti un ampio archivio storico di incidenti causati dalla fatica dei materiali, che hanno avuto purtroppo anche risvolti disastrosi.
Incidenti dovuti alla fatica
Uno di questi è avvenuto nel maggio del 1994 ad Imola, in cui perse la vita il pilota Ayrton Senna. L’incidente fu causato dalla rottura del piantone dello sterzo della sua vettura che, priva di controllo, finì fuori pista. Il piantone della vettura, fu precedentemente allungato. Questa modifica comportò il taglio del piantone e l’inserimento, con successiva saldatura, di un tubo di dimensioni più piccole. Nel corso del Gran Premio, le numerose sollecitazioni provocarono l’innesco e la propagazione di una cricca nella zona che precedeva la saldatura, portando alla rottura repentina del componente.

Un altro incidente, questa volta in ambito aereo, è quello avvenuto il 12 agosto 1985 al volo Japan Airlines 123 che causò 520 morti; l’incidente fu causato dallo squarcio in volo della paratia posteriore e dal conseguente danneggiamento del sistema idraulico di controllo del velivolo. La paratia posteriore subì un intervento di manutenzione non conforme, a seguito di un danneggiamento subito in un precedente atterraggio. L’errato intervento comportò una riduzione della vita a fatica del componente che, dopo circa 12000 cicli di pressurizzazione, arrivò a rottura.
Molti ricorderanno poi l’incidente avvenuto alla stazione di Viareggio il 29 giugno 2009 che causò 33 morti e 25 feriti, dovuto al deragliamento di un convoglio che trasportava cisterne contenenti GPL. La rottura e la fuoriuscita del gas provocò un incendio che divampò all’interno della stazione. Il deragliamento fu causato dalla rottura di un assile a seguito della propagazione di una cricca per fatica la cui presenza non fu individuata a causa della mancata o errata esecuzione dei controlli previsti per questo tipo di componenti.
Purtroppo quindi, malgrado siano passati quasi due secoli dai risultati di Woler, il problema della progettazione a fatica, che porta ad un corretto dimensionamento dei componenti e ad un’opportuna scelta dei materiali, dei tempi e dei metodi manutentivi, continua ad essere un aspetto spesso sottovalutato le cui conseguenze possono avere però risvolti disastrosi.