Spacer Fabrics 3D: preforme per materiali compositi rinforzati con tessuti
Sostituire i tradizionali pannelli sandwich per ridurre peso del veicolo e emissioni di CO2.
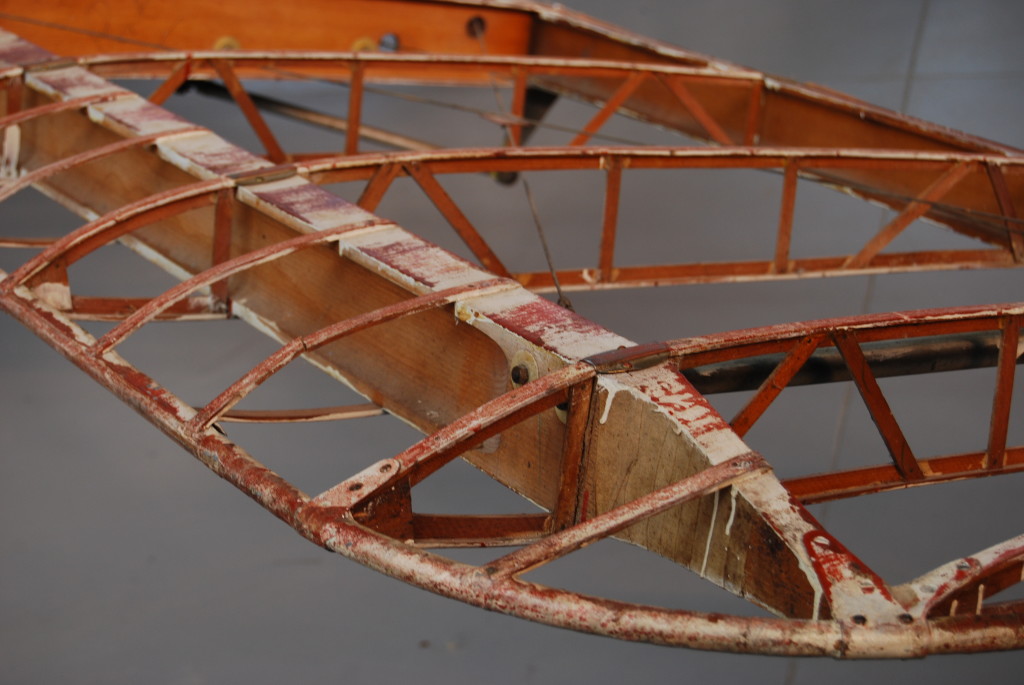
wikipedia.org
L’impiego dei tessuti nel settore aeronautico risale alla costruzione delle ali di aquiloni ed alianti adottati nei primi studi sul volo, e alla realizzazione dei primi palloni ad aria calda o idrogeno: le mongolfiere. Il primo volo con un mezzo motorizzato sostenuto con un essere umano a bordo è attribuito ai fratelli Wright, i quali si alzarono in volo nel 1903 con un aliante con struttura lignea, molto leggera, ricoperta con tela di raso in cotone. Successivamente, le iniziali strutture in legno hanno lasciato via via il posto alle costruzioni metalliche, che garantiscono maggiori prestazioni meccaniche e maggior durata nel tempo. Dalla Seconda Guerra Mondiale, gli americani hanno sempre associato l’idea di aerei metallici con il concetto di resistenza. Ma lo sviluppo, nella seconda metà del ‘900, di materiali compositi ha rivoluzionato il modo di pensare e progettare le strutture aerospaziali, tanto che oggi essi affiancano l’utilizzo predominante di leghe di acciaio e di alluminio.
Lo sviluppo dei materiali compositi è stato uno step importante anche per la riduzione delle emissioni di CO2. Infatti le emissioni nel mondo dovute alla combustione di combustibile per i mezzi di trasporto ammontano attualmente al 24% di quelle totali di origine antropica e sono ancora destinate ad aumentare. In particolare materiali compositi rinforzati con tessuti possono ridurre il peso dei veicoli (e di conseguenza il loro consumo) e la loro fabbricazione è ritenuta più economica, più veloce e più facile della fusione di alluminio e acciaio. Essi sono in genere costituiti da matrici polimeriche e come seconda fase: fibre ad alte prestazioni, ovvero fibre di vetro, di carbonio o aramidiche e per la loro produzione si possono realizzare preforme usando gli innovativi Spacer Fabrics 3D.
Gli Spacer Fabrics 3D sono costruzioni costituite da due strati piani esterni connessi da uno strato di collegamento, in genere realizzato da filati detti spacer, che rendono la struttura tridimensionale. Lo strato di collegamento interno è caratterizzato da alternanza di filati e spazi vuoti e garantisce che la struttura non sia schiacciata sotto l’effetto di una pressione esterna. Infatti, la distanza tra le due superfici viene mantenuta durante la compressione grazie alla resilienza del filato che le separa.
Per ottenere maggiore resistenza lungo la direzione z gli Spacer Fabrics tradizionali possono essere sostituiti da Spacer Fabrics in cui sono impiegati strati di tessuto come collegamento, anziché filati, i quali risultano notevolmente vantaggiosi per la costruzione di preforme tessili in compositi leggeri, grazie ad alcune proprietà quali la disposizione delle fibre in 3D, la possibilità di utilizzare differenti materiali, la riduzione della massa per volume, che dipendono da variabili come il materiale del filato, la distanza tra gli strati superficiali e la tecnologia adoperata per la costruzione del tessuto. Basso peso, buona resistenza a fatica e alla corrosione, associate ai bassi prezzi di produzione ed un processo di fabbricazione monostadio, fanno sì che le strutture che impiegano come preforme gli Spacer Fabrics 3D possano sostituire le tradizionali strutture sandwich, utilizzate ampiamente in campo aeronautico e automobilistico.
Queste sono costituite da due strati resistenti distanziati tra loro e collegati rigidamente da un elemento detto core (in genere un materiale caratterizzato da scarsa resistenza e bassa densità, come schiume o celle a nido d’ape). La loro maggior criticità riguarda la delaminazione, che provoca la separazione delle lamine con conseguente perdita delle proprietà meccaniche. Proprio la sostituzione dei tradizionali pannelli sandwich con Spacer Fabrics 3D nei quali le superfici esterne sono fortemente connesse l’un l’altra in quanto i filati che costituiscono i tessuti di collegamento sono intrecciati con gli strati superficiali, rappresenta una soluzione alle criticità dell’incollaggio tra pelli e core. Inoltre a causa della presenza di strutture solide e metalliche, i convenzionali pannelli possono risultare più pesanti degli innovativi pannelli ottenuti da materiali rinforzati con tessuti dotati di intercapedini e soffrire di difetti, quali la corrosione e la propagazione delle crepe.
In definitiva, l’impiego degli Spacer Fabrics 3D in sostituzione alle tradizionali strutture metalliche è finalizzato ad ottenere uguali o migliori prestazioni a vantaggio di una riduzione del peso e di emissioni di CO2. Nel 1989 NASA e Boeing hanno unito le forze per creare il programma “NASA Advanced Composites Technology” (ACT), per migliorare l’efficienza delle strutture in composito e ridurre i loro costi di fabbricazione. Infatti è stata costruita la macchina “Advanced Stitching Machine” (ASM) per realizzare strutture di ali in composito con un peso più leggero del 25 %, riducendo al contempo i costi di produzione e i costi di operazione delle compagnie aeree.
Image Credits: Mecit D., Marmarali A., 2012, Application of spacer fabrics in composite production, Usak University Journal of Material Sciences, 1, pp. 71 – 78; Abounaim Md., Process development for the manufacturing of flat knitted innovative 3D spacer fabrics for high performance composite applications, Dresden, Novembre 2010; www.kth.se; wikipedia.org.
Close-up Engineering – ©Tutti i diritti riservati