Freni ceramica: cosa sono, funzionamento e vantaggi
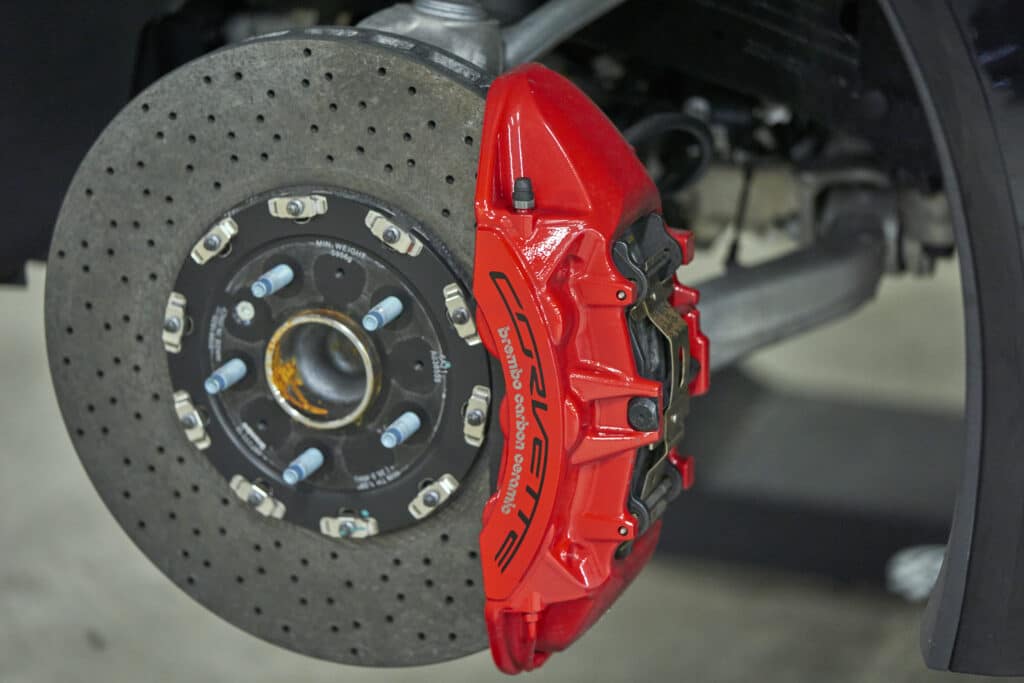
Freni in ceramica: cosa sono, come sono fatti e quali sono i vantaggi
I freni in ceramica ma in generale tutti i freni rappresentano una componente essenziale per la sicurezza di qualsiasi veicolo. Essi consentono di ridurre la velocità del veicolo o di fermarlo completamente, garantendo il controllo dello stesso e prevenendo incidenti o collisioni. La capacità di frenare in modo efficiente e affidabile è fondamentale per la sicurezza degli occupanti del veicolo, degli altri utenti della strada e per preservare l’integrità del mezzo di trasporto. Quando si guida, si possono verificare situazioni impreviste o di emergenza che richiedono una rapida risposta. In questi casi, i freni devono essere in grado di rispondere prontamente per permettere al conducente di fermare l’auto in modo tempestivo ed evitare conseguenze più o meno gravi. Una distanza di frenata più breve può fare la differenza tra una situazione di emergenza gestibile e un incidente catastrofico.
Caratteristiche dei freni
I sistemi frenanti moderni sono progettati per fornire prestazioni affidabili in una varietà di condizioni stradali e ambientali. Un sistema frenante efficace deve essere in grado di generare una forza di frenata sufficiente per fermare il veicolo in modo sicuro, anche su superfici stradali scivolose o bagnate. Ciò richiede una combinazione di componenti, tra cui dischi freno, pastiglie, pinze, liquido freni e il sistema di trasmissione della forza frenante. Inoltre, i freni devono essere in grado di dissipare rapidamente il calore generato durante la frenata. L’eccessivo surriscaldamento dei freni può portare a una riduzione delle prestazioni frenanti, noto come “fading“, che può compromettere la sicurezza del veicolo. Pertanto, i materiali utilizzati nella costruzione dei freni devono essere in grado di resistere a temperature elevate e di dissipare il calore in modo efficiente per garantire prestazioni costanti e affidabili.
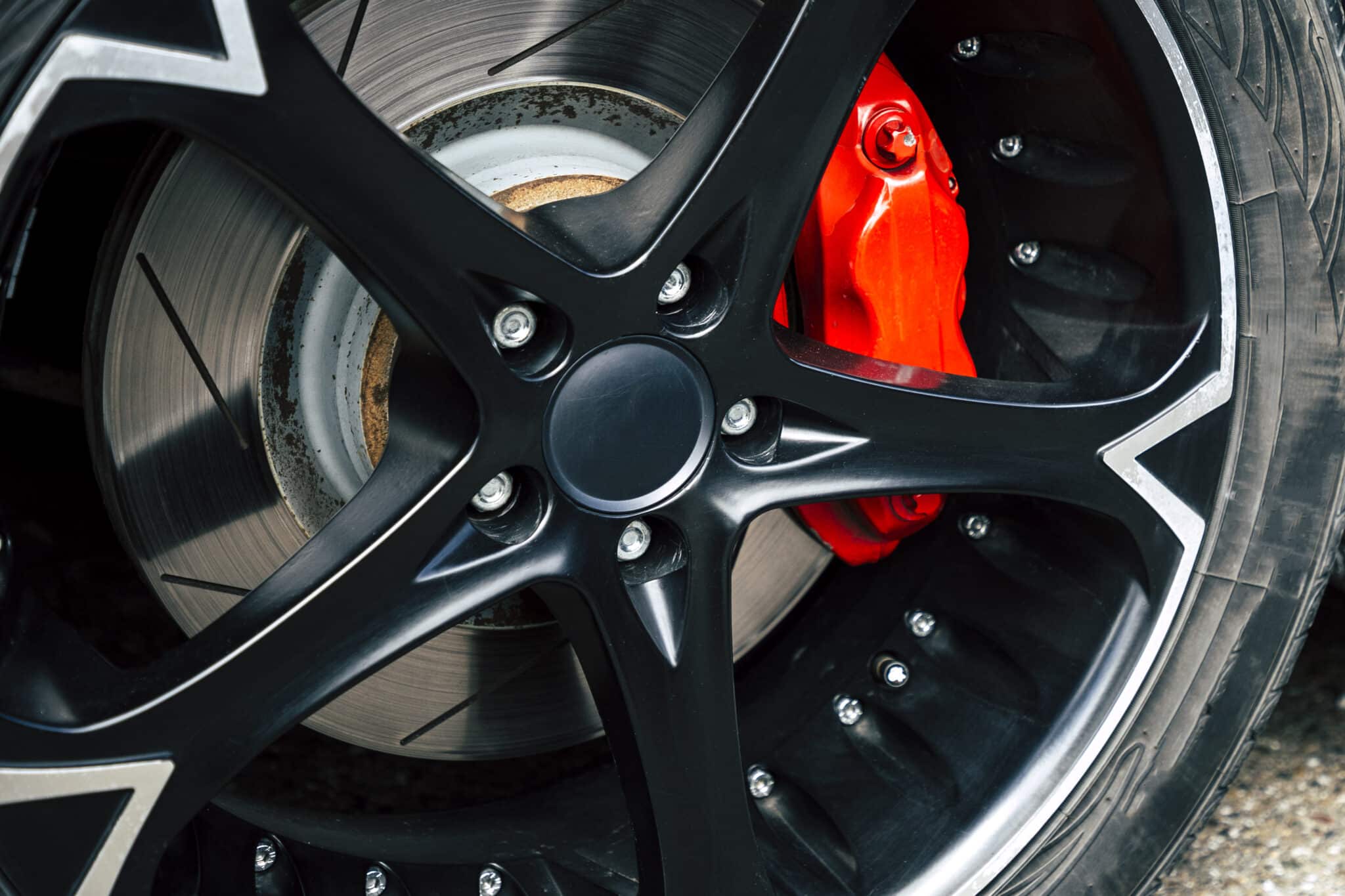
La manutenzione regolare dei freni è altrettanto importante per la sicurezza. I componenti del sistema frenante, come le pastiglie freno e i dischi freno, si consumano nel tempo a causa dell’attrito generato durante la frenata. Monitorare lo spessore delle pastiglie freno e lo stato di usura dei dischi freno è fondamentale per garantire che i freni siano sempre in grado di fornire le prestazioni desiderate. Inoltre, la purga e la sostituzione del liquido freni, che assorbe l’umidità nel tempo, contribuiscono a mantenere l’efficienza del sistema frenante.
Freni in ceramica: vantaggi ed applicazioni
I freni in ceramica, anche noti come freni a disco in ceramica o freni in carboceramica, sono un tipo di sistema frenante utilizzato in alcune vetture ad alte prestazioni e di lusso. A differenza dei freni convenzionali, che utilizzano dischi freno in acciaio, i freni in ceramica sfruttano dischi realizzati con materiali ceramici compositi ad alta resistenza.
La ceramica utilizzata per i dischi freno è solitamente composta da ossido di alluminio rinforzato con fibre di carbonio. Questa combinazione conferisce ai freni in ceramica una serie di proprietà desiderabili, come elevata resistenza termica, resistenza all’usura e leggerezza. I dischi freno in ceramica sono realizzati attraverso un processo di formatura e cottura del materiale ceramico ad altissime temperature. Questo processo conferisce al disco la sua struttura rigida e resistente. I dischi sono poi abbinati a specifiche pastiglie freno appositamente progettate per interagire con la superficie ceramica. I principali vantaggi dei freni in ceramica rispetto ai freni convenzionali sono i seguenti:
- Prestazioni di frenata superiori: i freni in ceramica offrono prestazioni di frenata notevolmente superiori rispetto ai freni convenzionali, consentendo distanze di frenata minori. Grazie alla loro elevata capacità di attrito e alla resistenza al fading, i freni in ceramica consentono una frenata più rapida ed efficiente, migliorando la sicurezza durante la guida;
- Peso ridotto: i freni in ceramica sono significativamente più leggeri rispetto ai freni convenzionali in acciaio. Questo contribuisce a ridurre la massa non sospesa dell’auto, migliorando la maneggevolezza e la reattività del veicolo. Inoltre, il peso ridotto aiuta a ridurre l’usura degli altri componenti della sospensione e delle ruote;
- Durata superiore: i freni in ceramica sono progettati per durare molto più a lungo rispetto ai freni convenzionali in acciaio. La ceramica è un materiale estremamente resistente all’usura e all’abrasione, il che si traduce in una maggiore durata delle pastiglie freno e dei dischi freno in ceramica. Ciò comporta minori costi di manutenzione e sostituzione nel lungo termine;
- Minore formazione di polveri e residui: generano meno polveri di attrito rispetto ai freni convenzionali, riducendo così l’accumulo di residui sulle ruote e sulle superfici circostanti. Questo aspetto aiuta a mantenere pulita l’auto e a ridurre l’impatto ambientale;
- Resistenza alle alte temperature: questi particolari tipi di freni sono notevolmente più resistenti alle alte temperature rispetto a quelli convenzionali. Ciò significa che possono sopportare temperature elevate senza subire danni o perdita di prestazioni, rendendoli ideali per situazioni di guida più intense o per veicoli ad alte prestazioni;
- Minore corrosione: poiché la ceramica è meno suscettibile alla corrosione rispetto all’acciaio, i freni in ceramica tendono a mantenere la loro integrità strutturale nel tempo, anche in condizioni climatiche avverse o in ambienti corrosivi;
- Estetica e lusso: i freni in ceramica conferiscono un aspetto distintivo ed elegante all’auto, particolarmente apprezzato dagli appassionati di automobili di lusso e di prestigio. La loro presenza può aggiungere un tocco di raffinatezza e stile al design complessivo.
Composizione e materiali dei freni in ceramica
I freni in ceramica sono realizzati utilizzando materiali ceramici compositi ad alta resistenza. La composizione chimica può variare leggermente a seconda del produttore e del tipo specifico di ceramica utilizzata. Tuttavia, in generale, questi tipi di freni sono costituiti principalmente da ossido di alluminio (Al2O3) rinforzato con fibre di carbonio.

L’ossido di alluminio, noto anche come allumina, è un materiale ceramico ampiamente utilizzato per la produzione di freni in ceramica. È caratterizzato da una struttura cristallina stabile e da una notevole resistenza all’usura e all’abrasione. L’allumina è in grado di sopportare temperature elevate e di mantenere le sue proprietà meccaniche anche in condizioni estreme. Le fibre di carbonio, invece, vengono utilizzate come rinforzo nella matrice di allumina. Queste fibre, realizzate in carbonio composito ad alta resistenza, forniscono un’ulteriore resistenza meccanica e termica al sistema frenante in ceramica. Le fibre di carbonio sono note per la loro elevata resistenza e leggerezza, contribuendo così a ridurre il peso complessivo dei freni in ceramica.
La combinazione di ossido di alluminio rinforzato con fibre di carbonio conferisce ai freni in ceramica la resistenza necessaria per sopportare le sollecitazioni termiche e meccaniche generate durante la frenata. Questi materiali ceramici compositi presentano una struttura porosa che permette una buona dispersione del calore generato durante la frenata, riducendo così il rischio di surriscaldamento dei freni. È importante notare che, a causa della natura composita dei freni in ceramica, la loro composizione chimica può variare leggermente da produttore a produttore. Alcuni produttori possono utilizzare altri materiali ceramici o additivi per migliorare specifiche proprietà dei freni in ceramica, come la resistenza al cracking o l’efficienza termica.
Funzionamento dei freni in ceramica
Andiamo a vedere nel dettaglio come funziona la fase di frenata. Quando il conducente preme il pedale del freno, viene generata una forza idraulica che viene trasmessa al sistema frenante. Questa forza viene applicata alle pastiglie dei freni, che vengono premute contro i dischi freno in ceramica. Le pastiglie dei freni, che sono realizzate appositamente per interagire con la superficie ceramica dei dischi, entrano in contatto con i dischi freno in ceramica. Le pastiglie esercitano una pressione sulle superfici dei dischi freno, generando attrito.
L’attrito generato tra le pastiglie dei freni e i dischi freno in ceramica converte l’energia cinetica del movimento in calore. Questo processo di conversione di energia riduce la velocità del veicolo. Durante la frenata, i dischi freno in ceramica sono in grado di dissipare rapidamente il calore generato. La composizione ceramica ad alta resistenza termica e la struttura porosa dei dischi consentono una buona dispersione del calore, evitando il surriscaldamento dei freni e mantenendo l’efficienza frenante.
L’attrito generato tra le pastiglie dei freni e i dischi freno genera una forza di resistenza che riduce la velocità del veicolo. Maggiore è la forza di attrito generata, maggiore è la capacità di frenata del veicolo. Quando il conducente rilascia il pedale del freno, la pressione sulle pastiglie dei freni diminuisce e i dischi freno in ceramica e le pastiglie si separano. Il veicolo può riprendere la sua marcia.

Effetto del riscaldamento sui freni e sulle prestazioni di frenata
A differenza dei freni tradizionali in acciaio, che possono già iniziare a lavorare a temperatura ambiente, i freni in carboceramica necessitano di un intervallo di temperature molto particolare e ben più alto: per funzionare al meglio, i freni carboceramici devono raggiungere una temperatura compresa fra i 600 e gli 800 gradi, con picchi anche intorno ai 1000 gradi. Al di sotto di queste temperature, in particolare al di sotto dei 300°C c’è il cosiddetto “congelamento”, in cui i dischi è come se fossero delle “lastre di ghiaccio” con un’efficienza di frenata molto, molto bassa.
I freni in ceramica raggiungono la massima efficienza frenante quando sono correttamente portati alla loro temperatura di esercizio, citata poco fa. Durante questa fase di riscaldamento, i freni carboceramici possono presentare una leggera diminuzione della prestazione frenante. Tuttavia, una volta raggiunta la temperatura operativa, offrono un’eccellente capacità di frenata. Portare i freni alla temperatura ottimale di esercizio aiuta a ridurre il rischio di fading, che è la perdita temporanea di prestazioni frenanti causata dal surriscaldamento. Sono, inoltre, progettati per gestire temperature elevate senza perdita significativa di prestazioni. La loro struttura ceramica e la capacità di dissipare rapidamente il calore consentono di mantenere un’efficienza frenante costante anche in condizioni di frenata intensa o prolungata.
Il riscaldamento dei freni ceramica può contribuire a migliorare la resistenza all’usura. Durante la frenata, il calore generato viene distribuito in modo uniforme su tutta la superficie del disco freno, riducendo così l’usura. La capacità dei freni in ceramica di gestire temperature elevate senza deformarsi o deteriorarsi consente una maggiore durata complessiva e una minore necessità di sostituzione. Possono anche sopportare rapidi cambiamenti di temperatura senza subire danni strutturali. Questa stabilità termica contribuisce a mantenere costanti le prestazioni frenanti anche in situazioni di frenata ripetuta o prolungata, evitando il deterioramento del materiale ceramico.
Componenti dei freni in ceramica
I freni in ceramica sono costituiti da diversi componenti che lavorano insieme per fornire un sistema frenante ad alte prestazioni. I principali componenti dei freni in ceramica includono:
- Dischi freno: sono il componente principale del sistema frenante. Sono realizzati utilizzando materiali ceramici compositi ad alta resistenza, spesso rinforzati con la fibra di carbonio. Questi dischi sono progettati per dissipare rapidamente il calore generato durante la frenata e offrire un’ottima capacità di frenata anche in condizioni estreme. Sono leggeri, resistenti all’usura e hanno una bassa conducibilità termica, che aiuta a ridurre la trasmissione di calore alle altre componenti del sistema frenante;
- Pastiglie: sono i componenti che esercitano la pressione sul disco freno per generare attrito e ridurre la velocità del veicolo. Sono realizzate utilizzando un composto ceramico ad alta resistenza, spesso combinato con altri materiali come metalli e resine. Le pastiglie freno offrono un’elevata capacità di attrito, una maggiore resistenza termica e una minore tendenza al fading rispetto alle pastiglie convenzionali. Sono progettate per garantire un’efficienza frenante costante e una durata più lunga;
- Calibri freno: sono i componenti che ospitano le pastiglie freno e si muovono per esercitare la pressione sul disco freno. Possono essere realizzati in diversi materiali, ma nei freni in ceramica sono spesso realizzati in leghe leggere ad alta resistenza. I calibri freno sono progettati per garantire una pressione uniforme e controllata sulle pastiglie freno, consentendo una frenata precisa e responsiva;
- Sensori elettronici: nei freni in ceramica può essere presente un sistema di sensori elettronici che monitorano la temperatura e le condizioni di frenata. Questi sensori possono fornire informazioni sulle prestazioni dei freni, il surriscaldamento e altre variabili importanti per garantire la sicurezza e l’efficienza del sistema frenante.
Il disco freno
Il disco freno in ceramica è realizzato utilizzando un processo di produzione complesso e specializzato. Esso è realizzato utilizzando un materiale ceramico composito ad alta resistenza, spesso chiamato carboceramica. Questo materiale è composto principalmente da polvere di ceramica, che può includere ossido di alluminio (Al2O3) e carburo di silicio (SiC), mescolato con fibre di carbonio. Questa combinazione conferisce al disco freno proprietà meccaniche elevate, come elevata durezza, resistenza alla trazione e resistenza all’usura. Il processo di formatura del disco freno inizia con la preparazione della miscela di polveri ceramiche e fibre di carbonio. Questa miscela viene compressa in una forma predefinita utilizzando pressature isostatiche o pressature unidirezionali. La forma compressa viene quindi sottoposta a un processo di sinterizzazione ad alta temperatura per unire le particelle e creare una struttura ceramica solida.
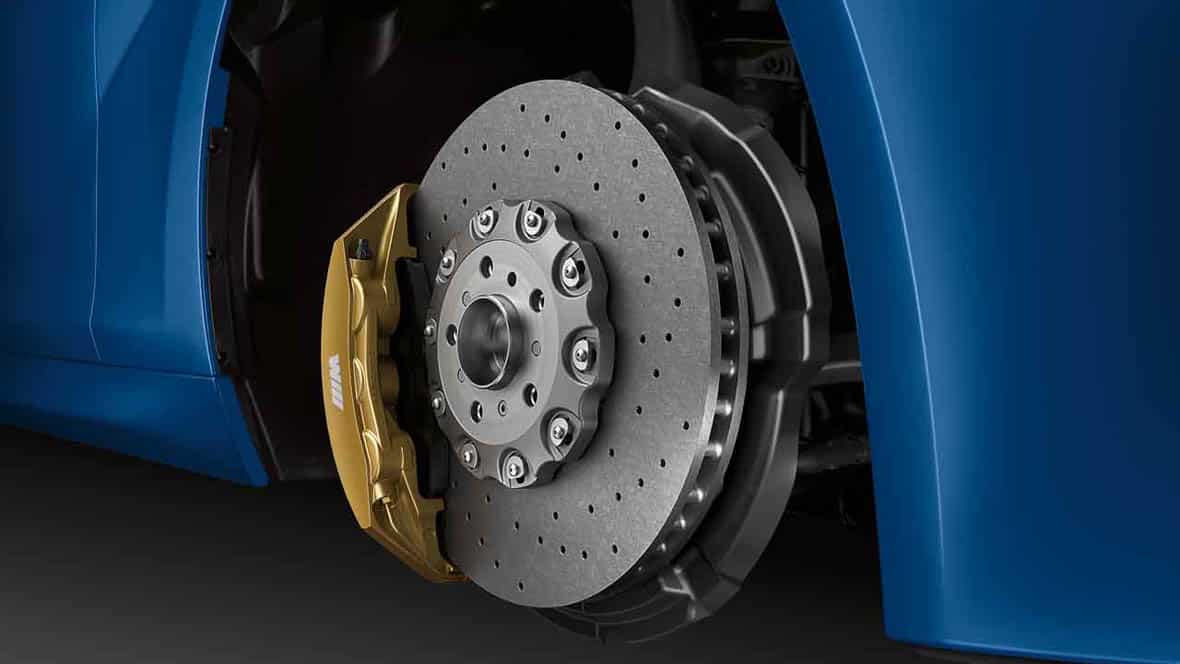
Dopo la sinterizzazione, il disco freno viene lavorato e rifinito per ottenere le dimensioni e le specifiche desiderate. Questa fase può includere operazioni come la rettifica della superficie, la fresatura dei bordi, la foratura dei fori di fissaggio e la lavorazione dei canali di ventilazione per migliorare la dissipazione del calore. È importante notare che la lavorazione del disco freno in ceramica richiede attrezzature e strumenti specializzati a causa della sua elevata durezza e fragilità. Dopo la lavorazione, il disco freno in ceramica può essere sottoposto a trattamenti termici per migliorarne le proprietà meccaniche e termiche. Questi trattamenti possono includere la ricottura, che riduce le tensioni interne nel materiale, e la tempra, che aumenta la durezza e la resistenza. In alcuni casi, il disco freno in ceramica può essere rivestito con un materiale protettivo per migliorarne la resistenza chimica e la resistenza all’usura. Questo rivestimento può essere realizzato utilizzando una vernice ceramica o una sottile pellicola protettiva.
Le pastiglie: differenza fra quelle sinterizzate e quelle organiche
Nel contesto dei freni in ceramica, le pastiglie sono generalmente realizzate utilizzando materiali organici o sinterizzati ad alte prestazioni. Queste pastiglie freno offrono prestazioni superiori rispetto alle pastiglie convenzionali. Le pastiglie freno organiche sono costituite da un mix di materiali, tra cui resine, fibre e riempitivi. Questi materiali sono solitamente meno abrasivi e possono includere ingredienti come grafite, polvere di metallo e fibre naturali. La presenza di componenti organici contribuisce a una guida silenziosa e un’usura ridotta dei dischi freno. Questi componenti vengono compressi e formati in una forma specifica per adattarsi al calibro del freno. Le pastiglie freno organiche sono apprezzate per la loro bassa rumorosità, buona modulabilità e capacità di attrito costante. Tuttavia, possono avere una maggiore usura rispetto alle pastiglie sinterizzate.
Le pastiglie freno organiche offrono una buona modulabilità, che consente un controllo preciso della frenata. Tendono ad avere una risposta iniziale più morbida, offrendo una sensazione di frenata più lineare. Tuttavia, possono avere una capacità di frenata leggermente inferiore rispetto alle pastiglie sinterizzate, specialmente in condizioni di guida ad alte temperature o in situazioni di frenata più intense.
Le pastiglie freno sinterizzate sono realizzate utilizzando un processo di sinterizzazione, che coinvolge la compressione e il riscaldamento di una miscela di polveri metalliche ad alta temperatura. Durante il processo di sinterizzazione, le particelle metalliche si fondono insieme, formando una struttura porosa che conferisce alle pastiglie freno sinterizzate una maggiore resistenza termica, una migliore durata e una maggiore capacità di attrito rispetto alle pastiglie organiche.
Le pastiglie freno sinterizzate offrono una capacità di frenata superiore rispetto alle pastiglie organiche, soprattutto in condizioni estreme. Sono in grado di sopportare temperature elevate senza perdere l’efficienza frenante e offrono una maggiore potenza frenante. Le pastiglie freno sinterizzate sono spesso preferite per un uso sportivo o per applicazioni che richiedono una frenata più aggressiva.
Alcuni dei prodotti più popolari
Le pastiglie freno ATE Ceramic sono un tipo specifico di pastiglie freno progettate e prodotte dall’azienda ATE, con l’utilizzo di un materiale ceramico avanzato. Queste pastiglie freno offrono prestazioni elevate in termini di frenata, durata e comfort acustico. Le pastiglie freno ATE Ceramic sono realizzate con una miscela di materiali ceramici ad alta tecnologia, combinati con leganti e resine termoindurenti. Questa composizione specifica conferisce alle pastiglie proprietà uniche di attrito, resistenza all’usura e dissipazione del calore.
Queste pastiglie sono progettate per ridurre il rumore e il fastidioso fenomeno dello stridio dei freni durante la frenata. Questo fornisce un’esperienza di guida più silenziosa e confortevole. Le pastiglie freno ATE Ceramic sono realizzate attraverso un processo di produzione preciso che coinvolge la formatura, la pressatura e la successiva cottura a temperature elevate. Durante la cottura, i materiali ceramici si fondono e si consolidano per creare una struttura resistente e omogenea. È importante notare che le pastiglie freno ATE Ceramic sono progettate per veicoli specifici e possono variare in termini di dimensioni e design per adattarsi a diverse applicazioni. È consigliabile consultare il manuale del proprietario del veicolo o fare riferimento alle specifiche fornite dal produttore delle pastiglie freno per garantire la corrispondenza e l’installazione corretta delle pastiglie freno ATE Ceramic sul proprio modello.
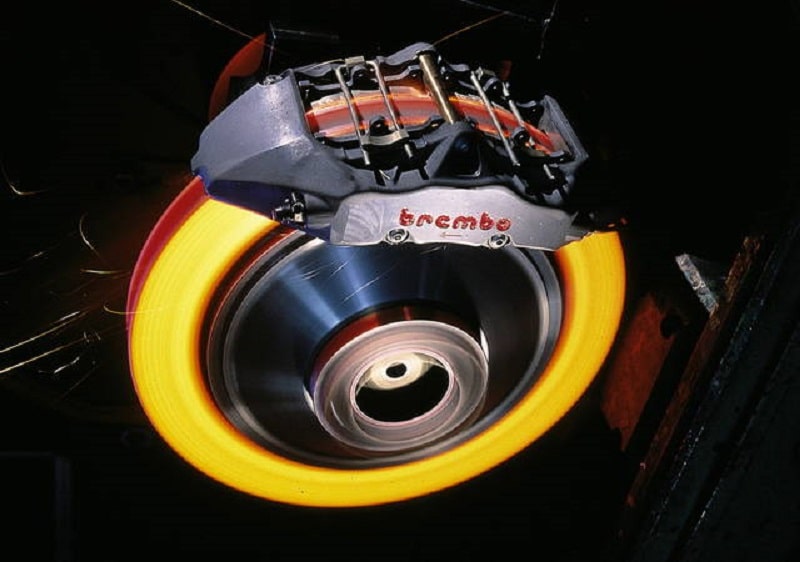
Durata e manutenzione dei freni in ceramica
I freni in ceramica, compresi i dischi freno e le pastiglie freno in ceramica, sono noti per la loro durata superiore rispetto ai freni convenzionali. Tuttavia, la durata effettiva dipende da diversi fattori come lo stile di guida, le condizioni stradali e l’uso del veicolo. Ecco alcune informazioni sulla durata prevista dei dischi freno e delle pastiglie freno in ceramica, nonché consigli per la manutenzione e il monitoraggio dell’usura:
- i dischi freno in ceramica sono progettati per essere molto resistenti all’usura e alla deformazione termica. In condizioni di guida normali, la durata prevista dei dischi freno in ceramica può superare i 100.000 chilometri. Tuttavia, se il veicolo viene utilizzato in modo più aggressivo o se si verificano situazioni di guida estreme, la durata potrebbe diminuire;
- le pastiglie freno in ceramica sono progettate per avere una durata superiore rispetto alle pastiglie freno convenzionali. In condizioni di guida normali, la durata prevista delle pastiglie freno in ceramica può variare da 60.000 a 100.000 chilometri. Tuttavia, anche in questo caso, la durata effettiva dipende da vari fattori e potrebbe diminuire in base allo stile di guida e alle condizioni di utilizzo;
- per garantire una lunga durata e prestazioni ottimali dei freni in ceramica, è importante seguire alcune pratiche di manutenzione:
- pulizia regolare: rimuovere la polvere e lo sporco accumulati sui dischi freno e sulle pastiglie freno in ceramica mediante una pulizia regolare. Questo aiuterà a evitare l’accumulo di detriti che potrebbero compromettere le prestazioni dei freni;
- ispezione visiva: controllare periodicamente lo spessore delle pastiglie freno in ceramica e l’usura dei dischi freno. Se le pastiglie freno sono consumate al di sotto dei limiti consigliati o se i dischi freno presentano solchi profondi o crepe, è necessario sostituire le parti interessate;
- manutenzione professionale: è consigliabile affidare la manutenzione e la sostituzione dei freni in ceramica a professionisti qualificati. Seguire le raccomandazioni del produttore del veicolo o del produttore dei freni in ceramica per garantire la corretta installazione e il corretto funzionamento del sistema frenante.
- è importante monitorare regolarmente l’usura dei freni per garantire la sicurezza e le prestazioni del veicolo. Alcuni segnali di avvertimento dell’usura dei freni includono:
- rumori anomali durante la frenata, come stridio o cigolio;
- distanza di frenata più lunga rispetto al solito;
- vibrazioni o pulsazioni nel pedale del freno durante la frenata (vibrazioni diverse a quelle del semplice azionamento dell’ABS);
- luce di avvertimento del sistema frenante accesa sul cruscotto. Se noti uno di questi segnali o se hai dubbi sull’usura dei freni in ceramica, è consigliabile far controllare il sistema frenante da un professionista.
Quali sono i migliori freni, quanto costano e quanto pesano
Per quanto riguarda il mondo dei freni, il marchio che li realizza è molto importante. Scegliere un produttore con una certa notorietà significa montare sul proprio veicolo un elemento per la sicurezza di qualità assoluta. Le migliori marche di pastiglie freni per auto sono Brembo, Bosch, TRW, Ferodo, ATE, Textar, STARK, Jurid, Lucas, PAGID e Remsa. Brembo lo avrai già sentito nominare: realizza l’impianto frenante per le auto di Formula 1, per le moto in MotoGP e altre categorie nell’ambito del motorsport estremamente importanti.
Il costo dei freni a disco in ceramica può variare in base a diversi fattori, tra cui il produttore, la dimensione, il modello del veicolo e il fornitore da cui vengono acquistati. In generale, i freni a disco in ceramica tendono ad essere più costosi rispetto ai freni a disco tradizionali in acciaio. Per un’auto stradale di fascia alta equipaggiata con freni a disco in ceramica, il prezzo medio può variare da qualche migliaio a diverse migliaia di euro. È importante notare che il costo potrebbe comprendere sia i dischi che le pastiglie.
Tuttavia, i prezzi possono variare notevolmente in base al marchio e al modello del veicolo, nonché alle specifiche esigenze e al mercato di riferimento. Chiaramente per avere maggiori dettagli sul prezzo, può tornare utile chiedere ad un rivenditore o un’officina specializzata. È importante considerare che, sebbene i freni a disco in ceramica siano più costosi inizialmente, offrono vantaggi come una maggiore durata, prestazioni di frenata superiori e una migliore dissipazione del calore. Tutto ciò si traduce in una migliore sicurezza: quindi, fondamentalmente è un investimento sulla propria incolumità e quella degli altri utenti della strada.
Come già anticipato ad inizio articolo, la leggerezza dei freni in ceramica è uno dei loro vantaggi principali, poiché contribuisce a ridurre il peso complessivo del veicolo, migliorando l’efficienza e le prestazioni. Il peso esatto dei freni a disco in ceramica può variare in base al modello specifico, alla dimensione e al design del disco freno. Tuttavia, in generale, i freni a disco in ceramica possono pesare circa il 50% in meno rispetto a quelli in acciaio.
Ad esempio, un disco freno in ceramica per un’auto stradale di dimensioni standard può pesare circa 5-7 kg, mentre uno in acciaio equivalente può pesare circa 10-15 kg. Questa riduzione di peso può contribuire a migliorare l’agilità del veicolo (considerando che di freni un’auto ne ha quattro, motivo per cui il vantaggio sul peso è da moltiplicare per quattro), la distribuzione del peso e l’efficienza del carburante.